Understanding the Fundamentals of Nylon Injection Molding
In the realm of plastic manufacturing, nylon injection molding stands as a pivotal technique, known for its versatility and strength. This method transforms nylon into diverse products, from automotive parts to everyday items, showcasing its durability and adaptability.
This article delves into the nuances of nylon injection molding, focusing on its most popular forms, PA6 and PA66, and the essential aspects of the molding process. Our exploration offers insights into this key manufacturing process, highlighting how modifications enhance nylon’s properties and its applications across various industries. Join us in uncovering the intricate world of nylon injection molding, a cornerstone of modern manufacturing.
Versality of Nylon Injection Molded Products
Nylon is so extensively used that nylon injection-molded products are almost everywhere in our daily lives. Below are some examples of nylon products, provided for a quick overview of their widespread applications.
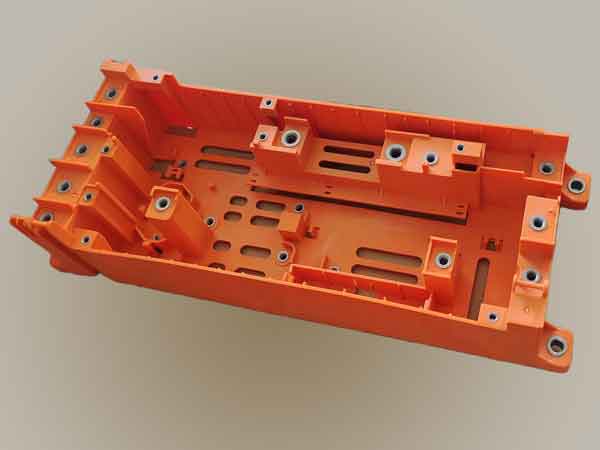
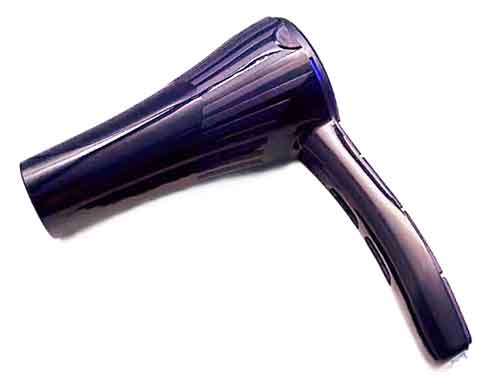
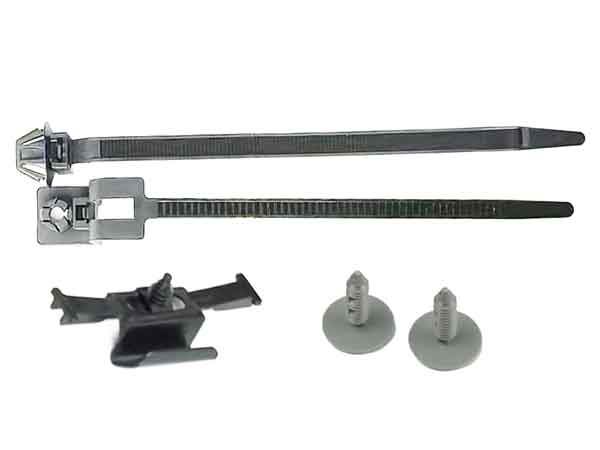
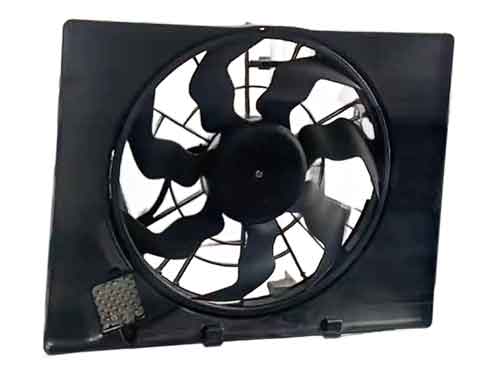
What is Nylon?
Nylon is a synthetic polyamide (abbreviated as PA), a type of polymer that is formed by amide bonds (-NH-CO-). It belongs to the family of semi-crystalline thermoplastic polymers. Known for its strength, toughness, high-temperature resistance, wear resistance, and low friction, nylon is widely used in textile manufacturing and injection molding processes. This material was invented and named by the American company DuPont in the late 1930s. Nylon was first used for toothbrush bristles and later expanded to the production of stockings, parachutes, and other items.
The name “nylon” is quite memorable, although there is no clear explanation for its specific meaning. Nonetheless, it stands as a successful example of commercial branding.
It’s important to note that while nylon is a type of polyamide, not all polyamides are referred to as nylon. For instance, natural materials like silk and wool are polyamides composed of amino acids, and certain aromatic polyamides also do not fall under the category of nylon.
Types of Nylon
The primary types of nylon are Nylon 6 and Nylon 66, which dominate the market. Nylon 6 is known as polycaprolactam, while Nylon 66 is polyhexamethylene adipamide. Nylon 66 is approximately 12% harder than Nylon 6. Following these are Nylon 11, Nylon 12, Nylon 610, and Nylon 612.
Additionally, there are types like Nylon 1010, Nylon 46, Nylon 7, Nylon 9, Nylon 13, and newer varieties such as Nylon 6I, Nylon 9T, and the specialty Nylon MXD6, which is known for its barrier properties. These diverse types of nylon offer a range of properties that cater to different industrial needs and applications.
Advantages and Disadvantages of Nylon
Nylon, a widely used synthetic material, has the following advantages and disadvantages:
Advantages:
- High Mechanical Strength: Nylon is known for its excellent strength and toughness, making it ideal for applications that require high mechanical strength. Its toughness further increases when it absorbs water.
- High-Temperature Resistance: Standard nylon can withstand temperatures above 100 ℃, and certain modified types can even endure up to 200 ℃.
- Smooth and Wear-Resistant Surface: Nylon’s surface is smooth with a low coefficient of friction, offering significant wear resistance. It exhibits self-lubricating properties when used as a part of moving machinery, reducing noise and eliminating the need for lubricants in low-friction applications.
- Corrosion Resistance: Nylon resists alkalis and most saline solutions well. It also withstands weak acids, motor oils, gasoline, aromatic hydrocarbon compounds, and general solvents. Nylon is inert to aromatic compounds and offers excellent resistance to gasoline, oils, fats, alcohol, and weak alkalis, along with impressive anti-aging properties.
- Good Electrical Insulation: Nylon maintains a certain level of electrical resistance, even in humid environments.
Nylon is Ideal for Metal Insert Molding Due to Its Strength
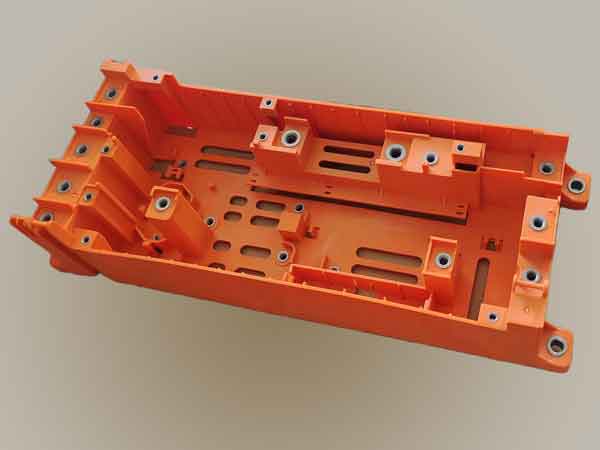
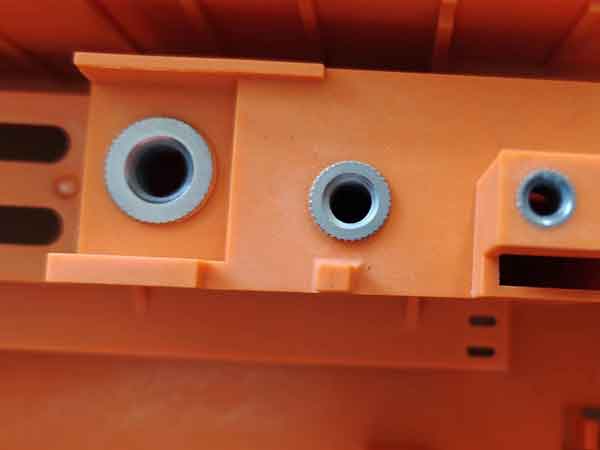
Nylon’s strength and toughness make it ideal for metal insert molding. The case features 34 embedded metal nuts. Since manually installing them exceeds 2 minutes, pre-heating the inserts is inefficient. Yet, the likelihood of plastic cracking is low, even with cool inserts.
Disadvantages:
- Water Absorption and Swelling: Nylon tends to absorb water, with an absorption rate exceeding 3%, leading to poor dimensional stability.
- Poor UV Resistance: Prolonged outdoor exposure can cause nylon to age and degrade.
- Limited Temperature Resistance: Nylon becomes brittle and loses strength in low-temperature environments, while it is prone to aging and degradation at high temperatures.
Therefore, when choosing nylon as a material, it is essential to consider these strengths and weaknesses to ensure its suitability and durability for specific applications.
Nylon 6 and Nylon 66 for Injection Molding
Since these two are the most commonly used types of nylon in injection molding, let’s compare them to understand their characteristics. Both belong to the polyamide family of polymers and share similarities in their molecular structures.
Similarities and Differences:
Semi-Crystalline Nature: Both are semi-crystalline plastics, but Nylon 66 has a higher degree of crystallinity than Nylon 6, leading to some differences in physical properties.
Density: The density of both Nylon 6 and Nylon 66 is around 1.10 to 1.15 g/cm3. However, incorporating glass fibers or other fillers can increase the density, typically staying below 1.5 g/cm3.
Melting Point: Nylon 66’s melting point is around 260 ℃, which is 20-40 degrees higher than Nylon 6. This gives Nylon 66 superior heat resistance, but it falls short in elasticity, toughness, and fatigue resistance compared to Nylon 6.
Toughness: Nylon 6 offers better toughness.
Hardness: Nylon 66 is harder than Nylon 6.
Viscosity and Molding: Nylon 6 has lower viscosity, making it easier to mold, and it yields a better surface gloss. However, it has a higher water absorption rate, with a saturation water absorption rate of around 10%. This high absorption can significantly reduce material performance, which needs to be considered in the design.
Temperature Resistance: Nylon 66 can withstand temperatures of about 180-190 degrees Celsius, which is 50-60 degrees higher than Nylon 6.
By understanding these differences and similarities, manufacturers and designers can make more informed decisions about which type of nylon is best suited for their specific applications, particularly in regards to injection molding processes.
Types of Modified Nylon
To overcome the weaknesses of nylon, various modified forms of nylon have been developed in the market. The most common modification methods include blending, filling, and copolymerization. Blending involves mixing nylon with other plastics or rubbers to complement each other’s strengths; filling modification typically adds materials like glass fibers, calcium carbonate, or talc to increase strength and reduce shrinkage; copolymerization modifies the molecular chain, grafting or segmenting other functional groups or polymers onto PA6 chains to enhance overall performance.
Here are some commonly used modified nylons:
Reinforced Nylon: Most reinforced nylon uses glass fibers, along with fillers like calcium carbonate and talc. These additives improve dimensional stability and hardness, but they can also increase the density and reduce the toughness and surface gloss of the material.
Toughened Nylon: The primary purpose of toughening with rubber is to enhance low-temperature performance. Regular nylon becomes brittle and loses functionality at temperatures between -30 to -20 degrees Celsius. Common toughening agents include EPDM rubber, EPR rubber, nitrile rubber, styrene-butadiene rubber, and polybutadiene rubber, with EPDM being the most widely used. However, toughened nylon can reduce material fluidity, making injection molding more challenging. It’s important to note that the use of toughening agents and flame retardants together may cause the flame retardants to become ineffective.
Wear-Resistant Nylon: Wear-resistant nylon is achieved by adding additives like carbon fibers, molybdenum disulfide, graphite, PTFE powder, or silicone powder to reduce friction or increase surface hardness, thereby reducing wear.
Flame-Retardant Nylon: Flame retardants on the market generally fall into three categories: halogenated, non-halogenated, and red phosphorus-based, though the latter is less common. Non-halogenated flame retardants are more environmentally friendly as they produce less smoke and fewer by-products when burning. Halogenated flame retardants are more efficient but produce black smoke and harmful gases when burning. It’s crucial to understand that flame-retardant plastics are not non-flammable but are designed to extinguish once the flame source is removed.
Transparent Nylon: Transparent nylon can achieve a light transmittance rate of over 90%, comparable to PMMA, and also possesses good tensile strength and impact resistance. The key to creating transparent nylon lies in altering the arrangement of polymer chains or introducing specific comonomers to reduce crystallinity, as the crystalline and amorphous regions are responsible for material opacity.
Additionally, there are other types such as electroplating nylon, UV-resistant nylon, etc., which are not detailed here. These modification techniques have significantly expanded the applications of nylon, meeting a wider range of industrial and everyday needs.
Key Considerations for Nylon Injection Molding
When it comes to nylon injection molding, several key methods and techniques must be mastered to ensure product quality. These include:

Drying Nylon Material: Nylon is prone to moisture absorption, so it’s crucial to dry it before injection molding. The recommended drying temperature is 120 ℃ for 4 hours. This step is different from some other plastics like PP, which do not require pre-processing drying.
Injection Molding Temperature:
PA6: The normal injection molding temperature range for PA6 is 220-260 ℃. It is generally recommended to set the second and third stage temperatures at 240-250 ℃, with the nozzle temperature controlled at 210-220 ℃. The temperature at the gate should be 10 degrees lower than the nozzle temperature, as too high a temperature may cause difficulty in material discharge and screw slippage.
PA66: The melting point of PA66 is around 255-260 ℃. The nozzle temperature should be adjusted to 265-275 ℃, and the second and third stage temperatures set between 280-290 ℃, with the gate temperature around 280 ℃.
Reinforced Nylon: For reinforced nylon (for both Nylon 6 and Nylon 66), it’s advisable to increase the injection molding temperature by 10-20 degrees due to its relatively poor flowability. To improve the appearance of the product, the temperatures of the second and third stages can also be increased by 10-20 degrees.
Injection Speed: When producing nylon products containing glass fibers, it’s necessary to increase the injection speed to prevent the appearance of floating fibers on the product surface.
Mold Temperature: For Nylon 6 and Nylon 66, the recommended mold temperature is 80-120 ℃. The mold temperature affects the surface quality and crystallinity of the product. Products with thinner walls require a higher mold temperature, while those with thicker walls can be processed with a lower mold temperature, such as 40-80 degrees.
More explanation on the mold temperature
Mold temperature plays a crucial role in determining the surface quality and crystallinity of products. A higher mold temperature results in better surface quality and also increases the product’s crystallinity. This happens because a higher temperature slows down the cooling process, giving the plastic more time to crystallize.
Increased crystallinity makes nylon products denser, more wear-resistant, harder, and increases their elastic modulus. It also reduces water absorption, making these products more suitable for applications where strength and rigidity are essential.
On the other hand, if you need your nylon products to be more flexible and stretchable, you should aim for lower crystallinity. This can be achieved by reducing the mold temperature. Lower temperatures speed up the cooling process, disrupting the crystallization process in the nylon material, and consequently lowering its crystallinity.
Tackling Floating Fiber on Nylon Surface
When injection molding glass-fiber-reinforced nylon, a common issue encountered is “floating fibers,” which are rough, patchy areas on the surface caused by the accumulation and surfacing of glass fibers.
To tackle floating fibers, the primary approach is to enhance the flowability of the nylon material, increase mold temperature, and boost injection speed and pressure. Another method involves adding a compatibilizer between the glass fiber and nylon material, although this tends to be more costly as it requires additional support from material suppliers and might reduce the nylon’s performance in other aspects.
Using Pure Nylon to Avoid Floating Fibers
Sometimes, even after taking all the measures mentioned above, it’s impossible to prevent minor floating fibers on the surface of the product, as shown in the pictures below:
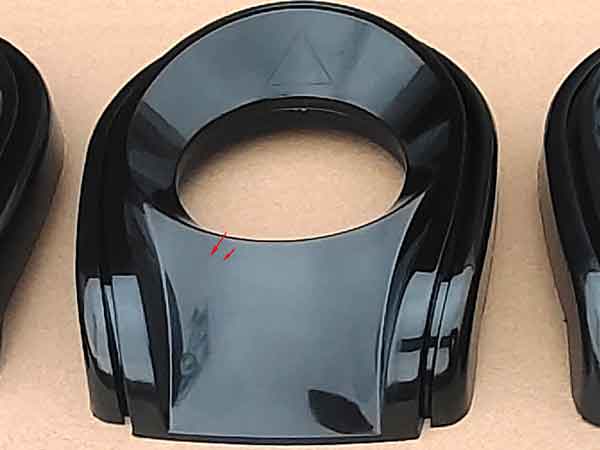
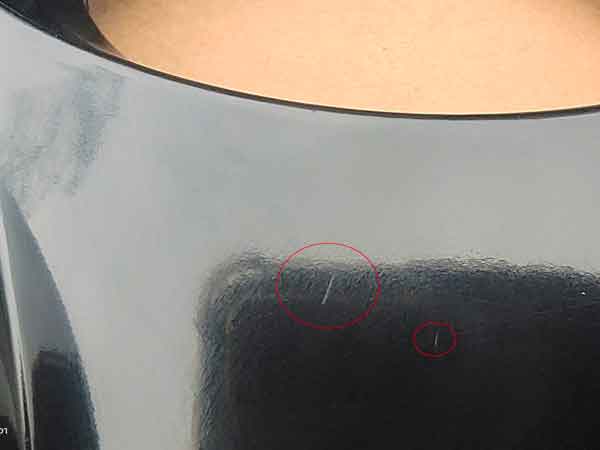
These floating fibers are generally acceptable in many cases, but for higher-quality products, they are not acceptable. In this case, you may need to opt for pure nylon. Of course, without the presence of glass fibers, the floating fibers will no longer be an issue.
However, pure nylon brings other challenges. It has a stronger adhesion to the mold, which can cause localized whitening and deformation when the product is ejected from the mold. Additionally, its shrinkage rate is higher compared to glass fiber-reinforced nylon, which can lead to the product’s size becoming smaller. These are additional problems that need to be addressed.
Why Many Small and Medium Enterprises Engage in Nylon Modification
Numerous small and medium-sized enterprises choose to engage in the modification of nylon, particularly PA6 and PA66, for several reasons:
Wide Application: Nylon’s excellent strength, wear resistance, chemical corrosion resistance, and high-temperature tolerance make it applicable in various fields such as automotive, electronics, machinery, and everyday goods. This diversity offers small and medium-sized businesses a broad market space.
High Potential for Modification: Nylon can be enhanced by adding different materials (like glass or carbon fibers), fillers (such as mineral fillers), and other additives (like flame retardants and UV stabilizers) to meet specific needs.
Ease of Processing: Nylon is easy to mold, and the cost of production and testing equipment is not high, which lowers the barrier to entry. The main cost is associated with the need for substantial production and storage space.
Cost-Effective: Nylon strikes a good balance between cost and performance. Small and medium enterprises can purchase raw materials at a lower cost and enhance product competitiveness through modification.
Stable Market Demand: The demand for nylon is relatively stable, providing small and medium enterprises with a predictable business environment, which is especially important for those with limited resources.
Mature Technology: Nylon modification technology is relatively mature, and the related processing methods and formulas are easily accessible, reducing technical difficulty and making it easier for small and medium enterprises to master.
Therefore, nylon modification is an ideal choice for small and medium-sized plastic factories, being technically feasible, economically reasonable, and adaptable to stable market demands. This helps them find a foothold in the fiercely competitive industry.
On-Site Visits to Small and Medium Material Manufacturers
When selecting and evaluating small and medium material manufacturers, an on-site visit to their factories is a crucial step. By being there in person, you can gain a direct understanding of whether their production process and storage management adhere to quality control standards. Such visits also allow you to inspect the quality of the raw materials used and verify if they are equipped with adequate testing equipment to ensure product quality.
Face-to-face communication with the manufacturers is also vital. Through conversations, you can assess whether they possess the professional knowledge and understanding necessary to guarantee product quality and subsequent service support. Additionally, interacting with their team members can give you insights into their work attitude and service awareness, which are important factors in choosing the right supplier.
To better illustrate this process, here is a video showcasing the production site of modified nylon. This video allows you to visually observe their production environment and operational processes, which is extremely helpful in assessing their production capabilities and product quality.
In summary, on-site visits not only provide you with first-hand information about the manufacturers but also help you make more informed and practical decisions. Such evaluations can strengthen your confidence in the supplier’s quality control and production capabilities, ensuring that your chosen partner can meet your business needs.
Material Performance Testing Experiments
Material manufacturing plants are usually equipped with various experimental equipment to test the performance of materials. These tests mainly include:
Tensile Strength Test (Including Elongation at Break): This test measures the material’s ability to withstand tensile forces. The results are typically expressed in megapascals (MPa). It also includes the elongation at break, which is the extent to which the material can elongate before breaking, usually expressed as a percentage (%).
Bending Strength Test: This test assesses the material’s performance under bending. It involves applying force to bend the material and measuring the required force and degree of bending, usually expressed in megapascals (MPa).
Impact Strength Test: This test evaluates the material’s resistance to sudden impacts. The results are expressed in kilojoules per square meter (KJ/m²), indicating the material’s toughness or resistance to impact.
Material Density Test: This test determines the material’s density, which is the mass per unit volume. The results are expressed in grams per cubic centimeter (g/cm³). The test involves weighing the material in air and water to determine its density.
Melt Flow Test: The melt mass-flow rate (MFR) or melt index (MI) measures how many grams of molten resin flow through a standard capillary tube under specific temperature and pressure conditions within a set time (typically 10 minutes), expressed in grams per 10 minutes (g/10min).
A video is provided here to demonstrate how these tests are conducted. In the video, you can see the actual testing process and equipment, which helps you better understand the specific operations and significance of each test.
These tests are crucial to ensure that materials meet the performance requirements for specific applications. With these detailed experimental data, manufacturers can accurately assess and improve materials, thus providing higher quality products.