Why are Injection Molding Tolerances Important?
In the production process of injection molded parts, variations in dimensions are inevitable due to influences from the mold, injection molding machine, materials, and environmental factors. Therefore, setting reasonable tolerances for product dimensions and ensuring they meet these tolerances is crucial. Appropriate tolerances can:
- Ensure that parts function correctly, especially when multiple components need to fit together;
- Guarantee product consistency and reliability;
- Reflect the manufacturing and management capabilities of the factory;
- Enhance corporate image and customer satisfaction.
Establishing appropriate tolerance values is essential. Tolerances that are too large or too small can lead to issues in product use and are indicative of a lack of knowledge in injection molding.
Sources of Dimensional Deviations in Injection Molded Parts
Dimensional deviations in injection molded parts mainly originate from two categories: molding process factors and mold factors. Here’s a detailed explanation and expansion of these factors:
Molding Process Factors
- Inconsistency in Plastic Materials: Different plastics exhibit varied flow, cooling, and shrinkage characteristics during molding. Poor consistency in materials can lead to dimensional inconsistencies within the same batch or across different batches.
- Control Accuracy of Injection Molding Machines: The precision of temperature and pressure control during the injection molding process directly affects the dimensional stability of the products. Fluctuations in temperature and pressure can lead to inconsistent final dimensions.
- Mold Temperature: Temperature control of the mold is crucial for molding quality. Uneven temperature or inaccurate control can result in uneven cooling of the parts, thereby affecting dimensional accuracy.
- Elastic Deformation of the Mold: Under injection pressure, the mold may undergo slight elastic deformation, indirectly impacting the dimensions and shape of the parts.
Mold Factors
- Manufacturing Precision of Mold Dimensions: The precision with which the mold is manufactured is a key factor in determining the dimensional accuracy of the final product. Slight deviations in the mold can be magnified during the molding process.
- Positional Accuracy of Movable Mold Components: For molds with movable components like sliders and ejector pins, the repetitive positioning accuracy of these parts inevitably impacts the consistency of the product dimensions. More details on this will be explained subsequently.
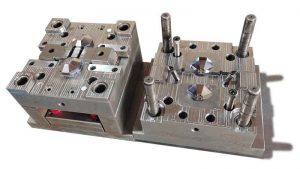
In conclusion, the issue of dimensional deviations in injection molded parts is complex and influenced by various factors, including material properties, equipment performance, and mold quality. In actual production, controlling the molding process parameters precisely, using high-accuracy molds, and optimizing material quality can effectively reduce dimensional deviations, thereby ensuring product quality and performance.
Common Standards for Injection Molded Parts
In the manufacturing and design process of injection molded parts, several standards are commonly referenced to ensure product quality and consistency. They are listed below for a quick reference:
- DIN 16901: This German standard specifically addresses the dimensional tolerances and deviations for plastic molded components, applicable to a variety of plastic materials used in injection molding.
- DIN 16742: It is a standard for general tolerances and acceptance conditions for plastic molded parts. It is applicable not only to injection molding but also includes compression molding and extrusion molding.
- GB/T 14486-2008: This is a national standard of China, covering the dimensional tolerance specifications for plastic molded parts, suitable for various plastic processing methods.
- Automotive Industry Standard QC-T-29017-1991: This specific standard for China’s automotive industry details the dimensional tolerances for plastic molded components within the automotive field.
- SAIC Standard MGR ES.22.PL.103: This is a corporate standard of SAIC Motor Corporation Limited in China, specifically guiding the dimensional tolerances in the design and manufacturing of plastic parts within the company.
- ISO 2768: This international standard is applicable to machined parts, including plastic components, where specific tolerances are not explicitly stated.
- JIS B 0401: This Japanese industrial standard, similar to ISO 2768, provides guidance for dimensions not specifically indicated with tolerances on mechanical engineering drawings.
- ISO 20457: This international standard offers a comprehensive guide to dimensional tolerances for plastic molded parts, applicable to various plastic processing methods.
Among these standards, ISO 2768 is perhaps the most well-known. However, it is a general standard for unspecified tolerances and is not specifically designed for injection molded parts.
A reasonable tolerance should reflect the realistic precision levels attainable in injection molded parts. Below, we will introduce the DIN 16901 standard in more detail.
Understanding the DIN 16901 Standard
1. Dimension Classification
In DIN 16901, tolerances are categorized into two types: TYPE A and TYPE B, specifically designed to address the characteristics of injection-molded parts. To better understand this concept, let’s explore the process of closing an injection mold, illustrated below:
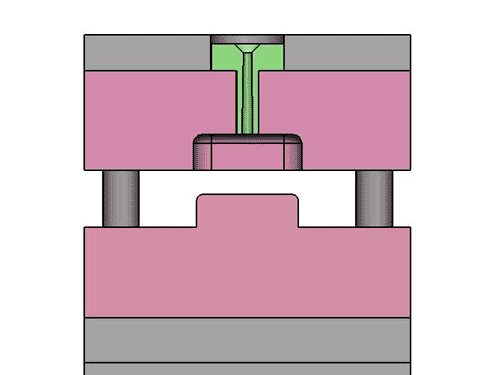
We observe that some dimensions on the plastic parts (Type B) are solely determined by the features on the upper and lower parts of the mold. These dimensions tend to change very little during the injection molding process.
In contrast, other dimensions (Type A), such as the thickness of the sidewalls and bottom, are determined after the upper and lower molds are closed. Since there might be some misalignment each time the molds close, this can lead to certain deviations. Therefore, a larger tolerance is allowed for these dimensions.
Type A dimensions also include sizes formed with the participation of moving parts like sliders and lifters.
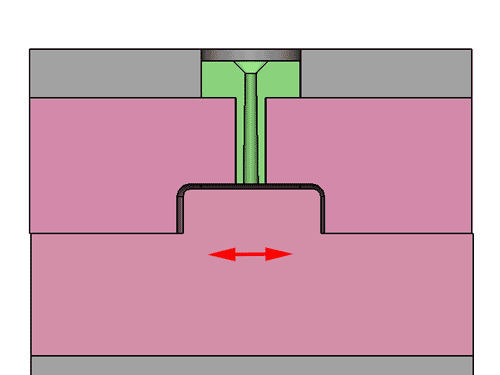
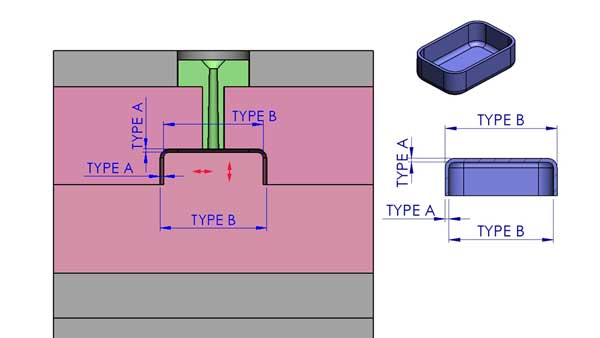
In other words, Type B dimensions are not affected by movable components within the mold. According to Figure 1 below, Type B dimensions are also known as mold-related dimensions in DIN 16901, essentially indicating the same idea.
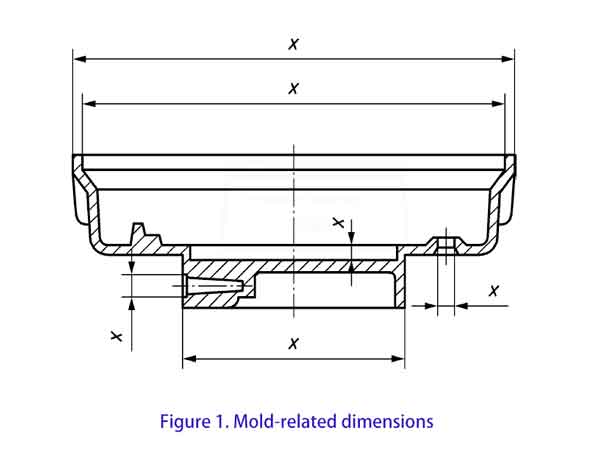
Type A dimensions however, as shown in the figure 2 below, are influenced by these movable parts, including the relative positions of the upper mold, lower mold, sliders, and lifters, which can result in minor dimensional deviations. Similarly, Type A dimensions are referred to as non-mold related dimensions in DIN 16901.
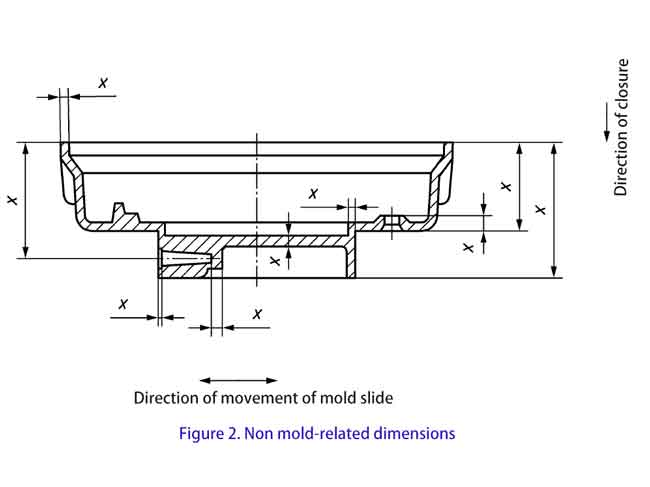
As mentioned above, the tolerances for Type A dimensions are generally larger than those for Type B, reflecting the realities of injection molding. Experienced injection molding or mold design professionals typically find it easy to distinguish between Type A and Type B dimensions.
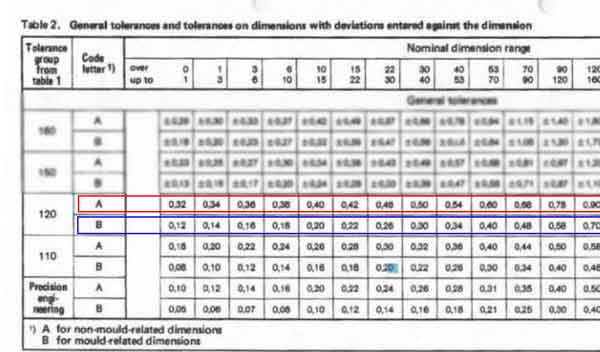
2. Impact of Material on Precision Level
- Different plastic materials have varying effects on the dimensional stability of the product. Some materials exhibit better dimensional stability, allowing for higher precision levels. The choice of tolerance levels must be based on the characteristics of the materials used.
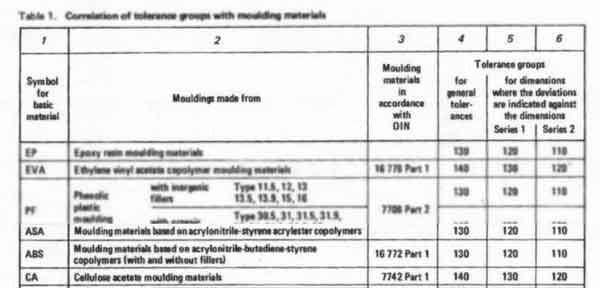
3. Linear Dimensional Tolerances Only
- The DIN 16901 standard primarily defines tolerances for linear dimensions, such as length, width, and height. However, it does not cover geometrical tolerances, like flatness or profile tolerances. Therefore, when considering the overall quality and precision of a product, it may be necessary to refer to other standards or industry practices for these aspects.
In summary, the DIN 16901 standard provides vital guidance on dimensional tolerances for the injection molding industry. It defines different tolerance levels based on the degree of dimension impact and the type of material used, but for form and positional tolerances, other standards should be consulted.
Selecting the Appropriate Tolerance Range
Choosing the right tolerance range is a crucial step to ensure accurate part fitting and functionality. Tolerances primarily consist of the nominal dimension and the upper and lower tolerances. Here’s a concise guide on how to select suitable tolerances for matching dimensions:
Understanding Tolerance Components
- Tolerance is made up of the nominal dimension and the upper and lower tolerances. The nominal dimension is the specified base size, while the upper and lower tolerances define the acceptable size range around the nominal dimension.
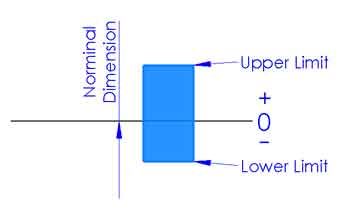
Choosing Dimension Range
- By referring to tolerance standards such as DIN 16901, you can determine a suitable size range for specific materials. These standards provide recommended tolerances for different types of dimensions, such as Type A and Type B dimensions.
Determining Nominal Dimensions
- Selecting the nominal dimension is a key step, though it often falls outside the guidance of tolerance standards. The choice of nominal dimensions should be based on design requirements, functional needs, and compatibility. For instance, if a part needs to fit tightly with other components, a more compact nominal dimension may be necessary.
Considering Practical Application
- When selecting tolerances, the part’s practical application environment should also be considered. For example, if the part will be used in environments with significant temperature variations, a larger tolerance range might be needed to accommodate thermal expansion or contraction.
Coordination and Verification
- After determining the tolerances, coordinate with the design team, production department, and quality control to ensure that the chosen tolerances are within manufacturing capabilities and meet product performance requirements. If necessary, conduct practical tests and verification to confirm the reasonableness of the chosen tolerances.
In summary, selecting the appropriate tolerance involves a comprehensive consideration of design requirements, material properties, processing methods, and real-world application environments, to ensure product quality and performance.
Let Us Help You Choose the Right Tolerances
Selecting appropriate tolerances is crucial for ensuring the quality and functionality of plastic parts. Given the softness and elasticity of plastics, accurately measuring their dimensions can be challenging. We offer our expertise to help you determine the suitable dimensional tolerance range. Here’s our approach and methodology:
Focusing on Key Dimensions
- For key dimensions that are critical to the product’s functionality and overall quality, we establish stringent tolerance ranges. We create specialized measuring tools, such as go/no-go gauges, to ensure precise dimension measurement.
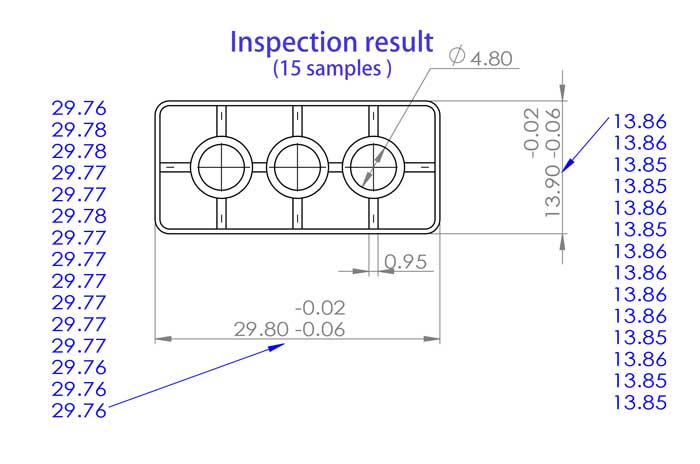
Handling Less Important Dimensions
- For less critical secondary dimensions, we typically use standard measuring tools like calipers. We also assess the fit of these dimensions using corresponding parts to ensure compatibility.
- Besides using fitting parts for measurement, we can also employ 3D-printed inspection tools for measuring dimensional accuracy. Although 3D printed products have lower accuracy, typically within +/- 0.1-0.2 mm, they are cost-effective and have short production cycles, making them suitable for applications with slightly lower precision requirements.
- Sometimes, we only guarantee the fit without providing specific tolerance values. As mentioned earlier, it’s challenging to measure plastic dimensions precisely, especially for softer materials like TPE, TPU, and silicone.
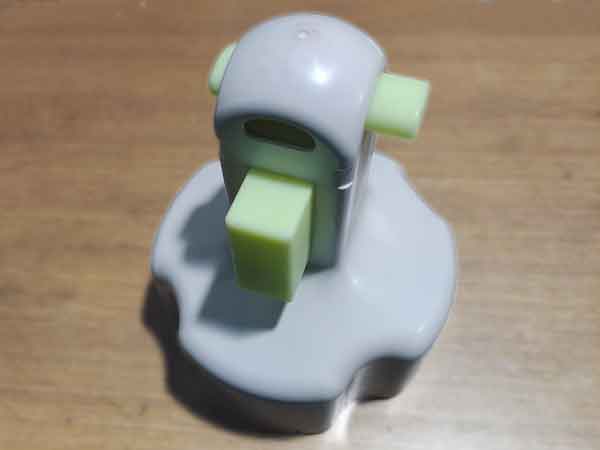
Information and Materials Required for Effective Tolerance Determination
To perform these tasks more effectively, we need the following information and materials from you:
- Specific Usage Scenarios of the Part: Understanding the environment and conditions in which the part will be used helps us more accurately determine the tolerance range.
- Samples of Matching Parts: If possible, providing samples of other parts that will be used in conjunction with the part in question can help us better assess and test the adaptability of tolerances.
Our goal is to help you determine the right tolerances in a cost-effective and efficient manner. This approach is particularly beneficial for small and medium-sized companies, as it can save time and costs while ensuring product quality.