Understanding Precision Injection Molding
When precision injection molding is mentioned, many people first think of the accuracy in product dimensions. Indeed, ensuring dimensional accuracy is a core element in precision injection molding, but that’s not all there is to it. In the process of precision injection molding, we are faced with a series of challenges and tests.
1. Firstly, controlling dimensional accuracy is a technical challenge. This includes the tolerance of part dimensions and geometric dimensioning and tolerancing (GD&T). This is primarily due to the shrinkage of plastic products during injection molding, which can also cause warping and lead to deviations in shape.
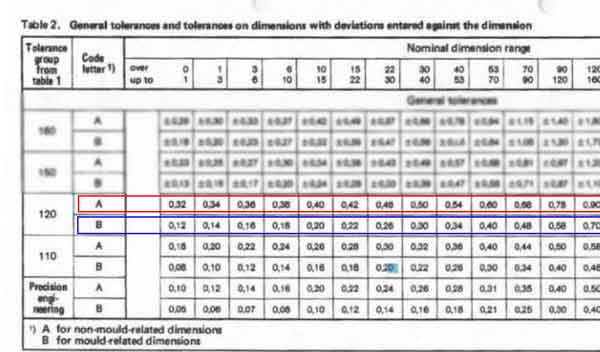
2. Secondly, injection-molded products often exhibit various molding defects, such as bubbles, flow lines, white and black spots, and so forth. These defects not only affect the appearance of the product but can also weaken its performance. To avoid these issues, it’s crucial to strictly control multiple factors in the injection molding process, including the material, injection speed, temperature, and pressure.
3. Additionally, controlling the wall thickness and the flow-length ratio is another challenge. Some products require very thin wall thicknesses, while others require thicker walls, posing higher demands on the precision of the injection molding machine. Especially when producing large or complex-shaped products, ensuring uniform wall thickness and flow-length ratio becomes a technical challenge.
In summary, precision injection molding is not just about dimensional accuracy. It also involves material selection, optimization of the production process, enhancement of equipment precision, and strict control of the production environment. Only by considering these factors comprehensively can we ensure the high quality and high performance of the final product.
Examples of Micro Injection Molding
Micro-injection molding products represent the pinnacle of precision molding technology. As products become increasingly miniature, the demands for their accuracy intensify. This technique requires extremely high machining precision and advanced equipment support to ensure that each tiny component meets the expected dimensional and functional standards. In this field, even the smallest improvement can significantly enhance product performance.
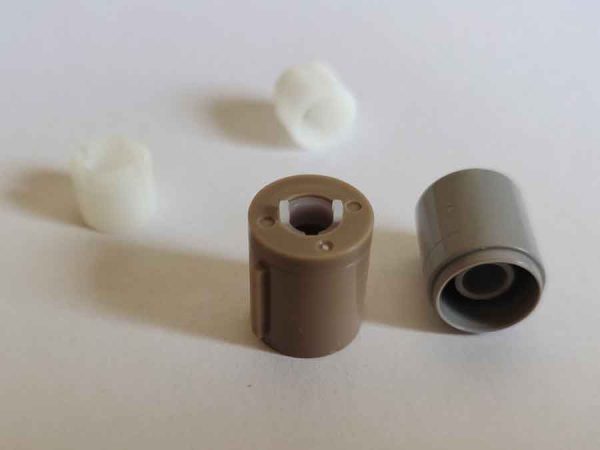


Two Aspects of Precision in Injection Molding
The accuracy of precision injection molding mainly involves two aspects:
- First, improving the accuracy of the injection mold,
- And second, enhancing the precision of the injection molding machine or the molding process itself.
If only an improvement in mold accuracy is required, and standard processes of a regular injection molding machine are used, it might suffice for the product’s requirements. This approach is usually less costly and less complex.
However, if there is a need to enhance the process accuracy of the injection molding machine as well, the challenge increases significantly. This would mean longer timeframes to resolve issues and increased costs. In short, the difficulty and cost of precision injection molding are closely tied to its accuracy requirements.
Key Features of Precision Injection Molds
High Precision Manufacturing Techniques
In mold manufacturing, the use of high-precision techniques such as high-speed milling, slow wire EDM (Electrical Discharge Machining), and mirror EDM ensures the quality and accuracy of mold processing. These methods eliminate the need for additional manual grinding or complex fitting processes. They make the mold surface smooth and highly accurate in fitting, effectively preventing defects like flash, even under high injection pressures.
Use of Hard Mold Materials
Generally, high-precision molds use hard materials with a hardness above HRC48, such as H13, S136, SKD61, 1.2344, etc. These materials not only ensure the durability and stability of the mold but also maintain high precision over long-term use, making them suitable for producing precision parts.
Conformal Cooling Technology
In some demanding injection molding processes, conformal cooling technology can cool products more precisely and efficiently. This technique uses special cooling channels inside the mold that closely conform to the shape of the product, achieving rapid and uniform cooling. This ensures dimensional accuracy of the product and improves production efficiency.
Intelligent Control with Built-In Sensors
To further enhance accuracy, some high-end molds are equipped with pressure and temperature sensors. These sensors can monitor key parameters during the injection molding process, such as pressure and temperature inside the mold cavity, and precisely control injection molding parameters to ensure product quality. This intelligent control not only improves product consistency and repeatability but also makes the production process more efficient and reliable.
Through these high-precision design and technical means, the importance of mold accuracy in injection molding production is further emphasized, providing a reliable guarantee for the production of high-quality precision components.
The Strengths of Precision Injection Molding Machines
Sometimes, merely enhancing the precision of injection molds is not enough to meet the product requirements. In such cases, precision injection molding machines are employed to improve product quality.
There are significant differences between precision injection molding machines and conventional ones, and these differences directly impact the quality and cost of the products.

(All-electric injection molding machines are becoming crucial in precision molding for their exceptional accuracy.)
1. High Injection Pressure
Grading of Injection Pressure The pressure in conventional injection molding machines typically ranges between 147~177Mpa, whereas precision injection molding machines operate at higher pressures of 216~243 Mpa, and even ultra-high-pressure injection molding machines can reach 243~392 MPa. Ultra-high-pressure injection molding greatly enhances the dimensional accuracy of the product by reducing the shrinkage rate to almost zero, but it also places higher demands on both the molds and the machines.
Effects of Injection Pressure One common issue with ultra-high-pressure injection molding is the potential backflow of molten plastic within the screw, which can degrade the quality of the plastic and the performance of the injection molded parts. To prevent this, ultra-high-pressure injection molding machines might adopt separated injection screws and plungers or special non-return valves. Additionally, higher injection pressures require greater clamping force, especially for larger-sized products.
Impacts on Plastic Molds Ultra-high-pressure injection molding imposes stringent requirements on molds. Not only do molds need to have smaller gaps to prevent flashing, but they also require higher processing precision and a good venting system. Moreover, the wear and tear on molds increases, necessitating higher hardness and wear resistance, which directly raises the manufacturing costs of the molds.
Effects on Production Cost While ultra-high pressure can reduce the shrinkage of plastic products and enhance their density and weight, it also means increased energy consumption and greater mold wear, leading to higher overall production costs.
Conclusion: Although ultra-high-pressure injection molding is a method to achieve precision in injection molding and indeed can provide higher dimensional accuracy and product quality, it comes at the cost of higher production expenses and technical demands.
Therefore, without specific requirements, ultra-high-pressure injection molding technology is not typically adopted casually. Instead, the choice of injection molding machine should be based on the actual needs of the product and the cost budget. The selection in precision injection molding should consider an integration of product requirements, cost-effectiveness, and technical feasibility.
2. High Injection Speed
Injection speed is a crucial metric for assessing the performance of injection molding machines. Conventional injection molding machines typically operate at speeds around 100mm/s, while high-speed machines far exceed this range, reaching speeds of 300mm/s to 1000mm/s, with some models even achieving higher speeds and an acceleration of the plunger exceeding 20G.
High-speed injection molding brings not only faster production efficiency but also higher injection pressure. This means that when using high-speed injection molding machines, one must confront challenges associated with high injection pressure. High-speed molding helps improve production efficiency and can effectively resolve certain defects in the injection process, such as flow lines and warping, thereby enhancing the overall quality of the product.
However, not all products are suitable for high-speed injection molding. The appropriate injection speed depends on the specific requirements of the product, including material properties, design complexity, and quality standards. Higher speed is not always better; the right speed selection should be based on a comprehensive consideration of product characteristics and production needs.
3. Precise Segmented Control of Speed, Pressure, and Flow
Accurate control of speed, pressure, and flow in the injection molding process is key to ensuring product quality. Segmental control of these parameters allows full utilization of their advantages and compensates for deficiencies, especially when dealing with complex or high-requirement products.
3.1 Segmented Injection Speed Control
Advantages of High-Speed Injection
- Reduces injection time, improving production efficiency.
- Increases flow distance, allowing materials to fill complex molds.
- Enhances the surface gloss of the product, improving appearance quality.
- Reduce weld lines, improving the structural integrity of the product.
- Reduces cooling deformation, ensuring dimensional stability.
Advantages of Low-Speed Injection
- Effectively prevents flash, maintaining clear product edges.
- Reduces flow marks, improving surface texture.
- Prevents mold trapping air and introducing air, reducing defects.
- Prevents molecular orientation deformation, maintaining physical properties.
Application of Segmented Control Different product requirements necessitate varying injection speeds. Simple structures might need only one or two speed segments, while complex, high-requirement products may require multiple segments.
By using different speeds at various stages of injection, one can optimize the filling process according to product characteristics and mold design, reducing defects such as weld lines, deformation, flash, and cracks, while also minimizing internal stress.
Precision injection molding machines are typically equipped with high-precision displacement sensors, ensuring speed control accuracy within 0.1mm, covering a wide range from very high to very low speeds.
3.2 Segmented Holding Pressure Control
Multi-stage Holding Pressure Strategy The holding pressure in injection molding is typically divided into several stages:
- The first stage reduces pressure to prevent flash.
- The second stage increases pressure to reduce shrinkage and improve dimensional accuracy.
- The third stage reduces pressure to minimize residual stress.
Role of Pressure Sensors Pressure sensors can be installed in multiple locations on the injection molding machine, such as the nozzle, hot runner system, cold runner system, and mold cavity, to measure and control the plastic pressure in real time. These data can be recorded and adjusted in real time, ensuring the appropriate pressure at each step, reducing defects, and facilitating post-molding inspection and troubleshooting.
The precision of injection and holding pressure control can reach within 0.1Mpa, ensuring precise application of pressure and high-quality molding.
In summary, precise segmented control of speed, pressure, and flow is an indispensable technology in precision injection molding. By finely adjusting these key parameters, product quality and production efficiency can be significantly enhanced, meeting the production needs of various complex and high-standard requirements.
4. Temperature Control
Temperature control is a crucial aspect of precision injection molding that cannot be overlooked. During the injection molding process, the temperatures of the barrel and nozzle need to be strictly controlled, often using a closed-loop control system to enhance precision. Currently, the temperature of the screw and barrel is frequently controlled using PID (Proportional, Integral, Differential) control, with an accuracy that can be maintained within ±1℃.
Additionally, the temperature of the mold is equally important, making mold temperature sensors a key to ensuring injection molding quality. Precise temperature control ensures that plastic materials are injected in their optimal state, leading to the production of products with stable quality and precise dimensions.
5. Customized Screws for Precision Injection Molding
In precision injection molding machines, the design of the screw is particularly crucial. These machines typically use screws designed for low shear to reduce shear heat in the material, effectively preventing excessive material overheating. To meet this design requirement, precision injection molding machine screws generally have a larger length-to-diameter ratio, usually between 24-30, resulting in a more slender form. This design helps enhance the screw’s processing capacity and the uniformity of the material. Additionally, these screws need to operate at higher rotational speeds.
For products and materials with special requirements, precision injection molding machines often use specialized screws, while conventional injection molding machines tend to use more general-purpose screws.
Furthermore, to better accommodate high injection pressures, the screws in precision injection molding machines are often made of alloy steel, ensuring their strength and durability under high pressure. In contrast, screws in conventional injection molding machines are commonly made of stainless steel. Overall, the role of the screw in precision injection molding machines is vital, as its design and material selection directly affect the quality of the products and the efficiency of production.
6. Mold Clamping Accuracy in Precision Injection Molding
In precision injection molding, the accuracy of mold clamping plays a crucial role in determining product quality. It requires the stationary mold (fixed template) and the moving mold (moving template) to have very precise repeat positioning, with the parallelism between them typically controlled within 0.06-0.08mm. To achieve such precision, several measures are adopted:
Enhancing Template Rigidity Utilizing high-rigidity templates can effectively improve the stability and durability of the mold, reducing deformation during high-pressure injection molding.
Using Large Linear Rails Employing large linear rails ensures the smooth and precise movement of the mold, thereby enhancing the accuracy of mold clamping.
High-Precision Nozzle Contact Mechanism Optimizing the nozzle contact mechanism prevents movement of the stationary mold caused by nozzle contact during the injection process, ensuring injection accuracy.
Strengthening Base Rigidity Using a high-rigidity base, such as one made from a single casting, can improve the stability and precision of the entire injection molding machine, maintaining high accuracy over long-term use.
Improved Mold Clamping Mechanism Improving the mold clamping mechanism, such as optimizing heat transfer, can eliminate the non-parallelism of the template caused by temperature variations, maintaining the precision of the mold.
In practical applications, such as in the manufacturing of smartphone lenses, these precise controls and optimizations can significantly enhance product quality. For example, they can reduce the offset of the geometric center of the top and bottom surfaces, reportedly to less than 1.12um. The fine control of mold clamping accuracy in precision injection molding is key to ensuring products meet high-quality standards.
Example: Mobile Phone Lenses
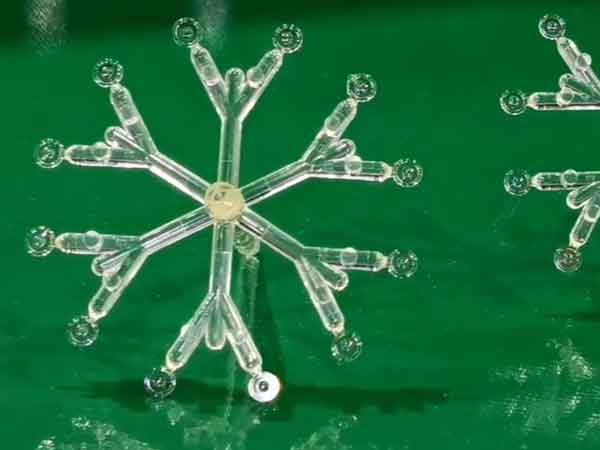
Mobile phone lenses, showcasing precision injection molding, incorporate advanced technologies to ensure high-quality production. Key techniques include:
- Material: APEL, a superior COC, enhances lens quality.
- Specialized Screw Design: Reduces defects like black and white spots, significantly lowering the defect rate from 10.7% to 0.1%.
- High Precision Locking Mechanism: Maintains the optical center’s offset within 1.12 micrometers, ensuring optimal lens performance.
- Injection Speed: A rapid speed of 550-600mm/s ensures uniform material distribution.
- Accurate V/P Control: Stabilizes pressure and temperature during injection to avoid flaws like flash.
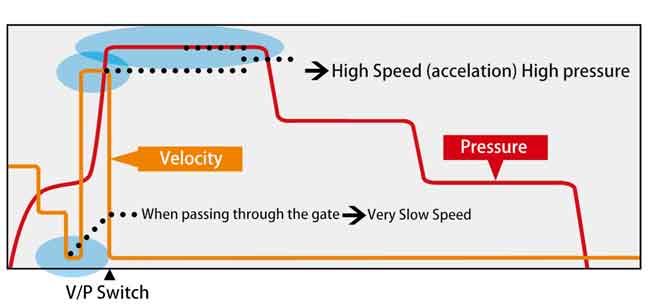
These technologies not only improve the lens quality but also demonstrate the manufacturing industry’s focus on precision and reliability.
Conclusion: Quality Standards of Precision Injection Molding
Precision injection molding sets higher quality standards in multiple aspects compared to conventional injection molding. These include the application of high speed and high pressure, precise segmented control of speed and pressure, as well as precise temperature control. Additionally, in terms of screw design and mold clamping mechanisms, precision injection molding demonstrates standards that surpass those of conventional injection molding.
However, the specific precision injection molding techniques required vary for different products. The principles discussed in this article are just basic guidelines. A deeper understanding and application of precision injection molding require analysis and research based on specific product cases. This means that precision injection molding is not just a fixed set of technical specifications but a complex process that needs to be flexibly adjusted and optimized according to specific application scenarios.