Understanding Injection Mold Steel Materials
Injection molds are indispensable tools in the manufacturing of plastic products. With technological advancements, plastic items ranging from utensils to car parts have become ubiquitous in every aspect of our lives. These products are predominantly created through the injection molding process, which involves heating plastic until it melts, injecting it into a mold, and then cooling it to form the various shapes and sizes we need.
The quality of the mold is directly linked to the quality of the plastic products, making the choice of high-grade mold steel crucial. Superior mold steel must withstand:
- Prolonged high-pressure conditions,
- The high-speed impact of molten plastic at high temperatures.
- Moreover, the molds are used repetitively, often millions of times, This necessitates mold steel to possess exceptional wear resistance, corrosion resistance, and adequate toughness.
Causes of Injection Mold Damage
Before delving into the required characteristics of mold steel, it’s important to understand how molds typically get damaged:
Mold Deformation Molds operating under repeated high-temperature and high-pressure conditions tend to deform over time. Specifically, the cavity of the mold may become indented, affecting the dimensional accuracy of the molded product and potentially leading to the formation of flash (excess material).
Wear and Tear The clean (sharp) edges of the mold gradually become blunt with prolonged use, leading to rounded corners and depressed surfaces. The most significant outcome of this wear is the production of flash.
Fracture After a period of use, molds can develop cracks due to material fatigue. These cracks tend to expand over time and with continued use, which can eventually lead to the fracture of certain parts of the mold.
Corrosion When acidic plastic materials or materials that release corrosive gases during processing (such as PVC and POM) are used, the mold surface may corrode over time. This corrosion can create uneven surfaces known as pitting, which can adversely affect the appearance of the final product.
Basic Requirements for Mold Steel Materials
Hardness, Wear Resistance, and Toughness The hardness and wear resistance of steel are crucial in mold manufacturing. This is because molds are subjected to continuous wear from molten plastic during the injection process, especially when the plastic contains hard fillers like glass fibers, which can cause more damage. Additionally, molds endure impacts during operation, necessitating a certain level of toughness to prevent cracking. When dealing with high-temperature plastics, the demand for wear-resistant steel intensifies, calling for the use of high-performance mold steel.
Polishing Performance High-quality mold steel should have a high purity level with a fine, uniform structure to ensure a flawlessly polished mold surface. The presence of pores, impurities, or other defects on the mold surface can adversely affect the appearance of the final product. For instance, S136 steel is renowned for its exceptional polishing properties.
Weldability Molds inevitably experience wear and accidental damage during use, and sometimes adjustments are needed due to design changes. The weldability of mold steel is thus extremely important as it determines the ease and feasibility of mold repairs and modifications.
Corrosion Resistance For molds processing corrosive plastics, the use of corrosion-resistant steel is essential. Common corrosion-resistant steels include S136, 2316, 420, 2083, and M333. Moreover, for molds frequently changing production batches, excellent corrosion resistance can reduce the need for rust-prevention maintenance.
Minimal Deformation in Heat Treatment During heat treatment, mold steel hardens, increasing the difficulty of machining and thereby the cost. To improve production efficiency and reduce costs, it is necessary to use steel materials with uniform internal structures that exhibit minimal deformation during heat treatment. Such materials will not develop excessive internal stresses or deformities, ensuring the precision and longevity of the mold.
In summary, selecting the appropriate mold steel material is crucial not only for ensuring the quality of plastic products but also for enhancing the durability of the molds, reducing production and maintenance costs, and improving the efficiency and economics of the entire production chain.
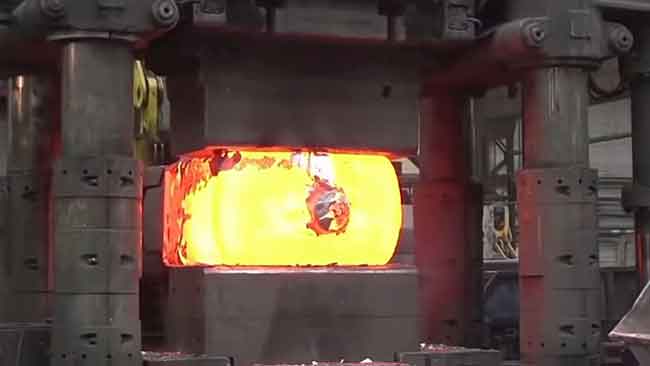
Pre-hardened vs. Through-hardened Mold Steel
Why Pre-hardened Mold Steel?
Typically, molds require overall hardening or surface hardening to achieve hardness levels between HRC50-60. This hardness range increases machining difficulty and cost.
Reaching such hardness necessitates heat treatment, which, especially in the case of complete quenching, poses a risk of deformation and prolongs the manufacturing cycle. Thus, pre-hardened mold steel was developed, typically having a hardness between HRC30-40 — a range that’s more manageable in terms of machining but sufficiently hard for many plastic injection molds, like PP, PE, ABS and so forth.
Pre-hardened Mold Steel
Pre-hardened mold steel is steel that has already been hardened before leaving the factory. Its hardness generally meets usage requirements, meaning it can be used directly in mold machining and production without the need for additional heat treatment by the user.
The main advantage of this type of steel is its convenience, as it saves on production time and costs by reducing the risk of dimensional distortion during heat treatment. Pre-hardened mold steel is typically used for shorter production cycles and smaller batches or when the size of the mold makes heat treatment impractical.
Common grades of pre-hardened mold steel include: P20, 718/718H/718HH, 738H, NAK80, S136H, and 2083H.
Through-hardened Mold Steel
Conversely, through-hardened mold steel is supplied in a softened state and requires heat treatment during or after the mold manufacturing process to achieve the desired hardness. The hardness of this steel can be precisely controlled through heat treatment, resulting in higher wear resistance and toughness.
Hardened mold steel is suitable for molds that need to operate over long periods and withstand high wear, especially in mass production of identical plastic products. However, the need for post-production heat treatment can increase production costs and requires careful handling to prevent deformation and stress issues due to uneven heating or cooling.
Regular grades of through-hardened mold steels are: 2083, S136,H13, SKD61,8407, and SKD11
In summary, both pre-hardened and through-hardened mold steels have their advantages and disadvantages. The choice between them depends on specific production needs, mold design, and economic efficiency. Pre-hardened mold steel offers convenience and speed, ideal for small batches or specific-sized molds; whereas hardened mold steel is more suitable for large-scale production molds that require very high wear resistance and long-term use.
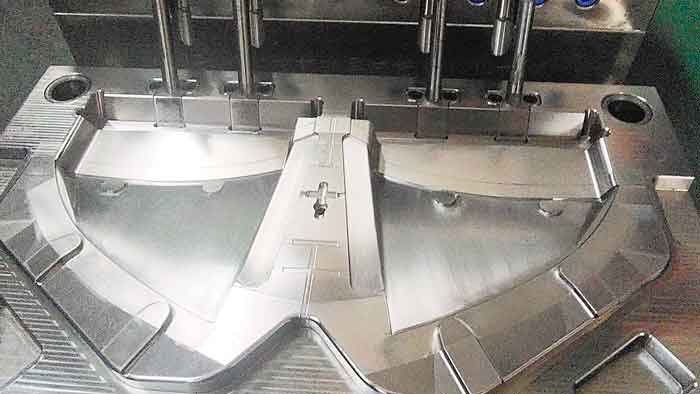
Common Mold Steel Types
There are hundreds of types of mold steel, but the ones listed below are among the most commonly used.
Different mold factories may prefer certain types over others, depending on their familiarity with these materials and the availability of reliable suppliers.
The following table lists the frequently encountered mold steel types.
Name | Heat treatment | Hardness | Brief description | Standard origin |
---|---|---|---|---|
P20 | Pre-hardened | HRC28-32 | Medium carbon Cr-Mo series plastic mold steel, excellent processing and polishing performance, affordable, suitable for products with low requirements and small production. | AISI USA |
718 | Pre-hardened | HRC30-34 | Cr-Ni-Mo series mold steel, an improved version of P20 (corresponding to American grade P20+Ni), with better hardenability, capable of making larger molds. The mold life is 2-3 times that of P20. | Assab Sweden |
718H | Pre-hardened | HRC34-38 | 718H has higher hardness and better mirror polishing than 718. The main difference between the two is the content of manganese and molybdenum. | Assab Sweden |
718HH | Pre-hardened | HRC36-40 | The hardness of 718HH is higher than that of 718H. | Assab Sweden |
738(1.2738) | Post heat-treated | HRC48-52 recommended | 738 has higher contents of Mn, Cr, Ni than 718, with good hardenability and toughness. It is the abbreviation of German standard 1.2738, while 718 is named by Swedish Assab. | DIN Germany |
2344(1.2344) | Post heat-treated | HRC50-54 recommended | Cr-Ni-Mo series mold steel, corresponding to American grade P20+Ni and 718, with better hardenability, capable of making larger molds. | DIN Germany |
S136 | Post heat-treated | HRC48-52 recommended | With a chromium content of 13.6%, it has high corrosion resistance and features a pure and fine structure, excellent polishing performance, as well as wear resistance, machinability, and good dimensional stability during hardening. | Assab Sweden |
S136H | Pre-hardened | HRC30-35 | Pre-hardened material of S136, no subsequent heat treatment required. | Assab Sweden |
2083(1.2083) | Post heat-treated | HRC50-54 recommended | German DIN standard, abbreviation of 1.2083, with a chromium content of 12.5-14.5%, corresponds to S136. It possesses good corrosion resistance, wear resistance, hardenability, and machinability for plastic mold steel. | DIN Germany |
2083H | Pre-hardened | Pre-hardened material of 2083. | DIN Germany | |
420 | Post heat-treated | HRC50-52 recommended | With a chromium content of 13.5%, corresponds to grade S136. It has good corrosion resistance, wear resistance, hardenability, and machinability for plastic mold steel. | AISI USA |
NAK80 | Pre-hardened | HRC37-43 | Added Ni-Al-Cu, good machinability and electrical discharge machining performance, excellent weldability, after gas nitriding the surface hardness reaches 750HV, achieving an extra-long mold life. | Diado Japan |
8407 | Post heat-treated | HRC48-52 recommended | Contains Cr-Mo-V hot work alloy mold steel, with good wear resistance, toughness, and ductility, stable machinability and polishability, excellent high-temperature strength and thermal fatigue resistance, good hardenability and minimal heat treatment deformation. | Assab Sweden |
H13 | Post heat-treated | HRC50-54 recommended | Contains Cr-Mo-V hot work alloy mold steel, the corresponding grade to 8407. | AISI USA |
SKD61 | Post heat-treated | HRC50-54 recommended | Contains Si-Cr-Mo-V medium alloy hot work mold steel, the corresponding grade to 8407. | Diado Japan |
Viking | Post heat-treated | HRC52-54 | Good dimensional stability in heat treatment; good machinability and grinding resistance; excellent toughness and wear resistance. | Assab Sweden |
2316(1.2316) | Post heat-treated | HRC32-36 | Contains Cr-Ni-Mo mold steel, highly corrosion-resistant, high-polish pre-hardened plastic steel material with good machinability and polishability. | DIN Germany |
Common Mold Steel Heat Treatment and Surface Treatment Methods
In addition to pre-hardened mold steels, most other mold steels require some form of heat or surface treatment to enhance their performance characteristics, such as strength, hardness, wear resistance, and corrosion resistance. These treatments ensure the mold can withstand the high pressure, temperature, and corrosive environment encountered during the injection molding process, especially if the mold will be used for producing large quantities of products.
Heat Treatment Methods for Mold Steel
The primary heat treatment methods for mold steel include quenching (followed by one or two tempering cycles to relieve stress, achieving high overall hardness while maintaining a degree of toughness), and tempering (a combination of quenching and high-temperature tempering, which results in better overall strength and toughness, though the hardness is lower than quenching). However, tempering is not frequently used for injection molds since they typically do not experience significant impact forces.
Not all mold steels can undergo quenching, and the required hardness after quenching varies depending on the type of steel. The ideal quenching hardness for different steel grades is provided in the above table, but specific requirements depend on each application and the recommendations provided by the mold steel supplier.
Surface Treatment Methods for Mold Steel
Surface treatments offer a wide range of options, including plating, nitriding, carburizing, carbonitriding, PVD (Physical Vapor Deposition), CVD (Chemical Vapor Deposition), and localized laser quenching. Among these, nitriding is the most commonly used.
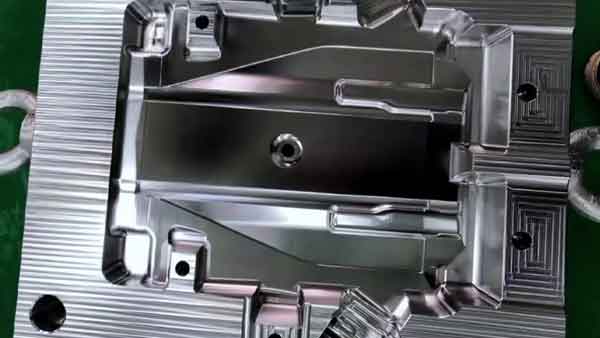
What is Nitriding?
Nitriding is a surface treatment where nitrogen atoms or ions are introduced into the surface layer of the metal, forming nitrides. This improves the material’s hardness, wear resistance, and corrosion resistance. Elements such as aluminum, chromium, vanadium, and molybdenum aid in forming stable and uniform nitrides. Therefore, steels suitable for nitriding typically contain these elements.
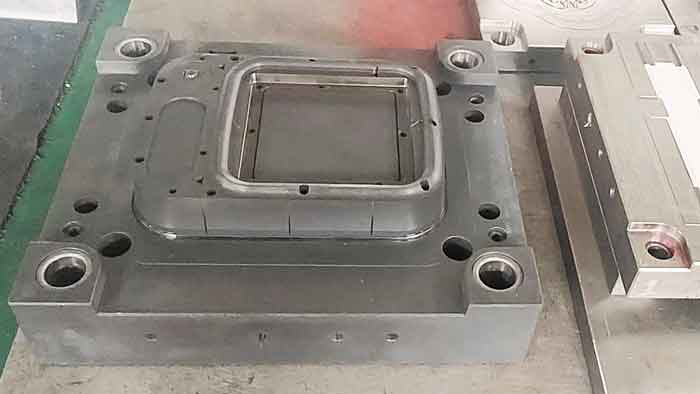
Hardness and Depth of Nitriding
The hardness of the nitrided layer typically reaches above 400 HV, with a depth that usually does not exceed 0.5 mm, as deeper penetration becomes increasingly challenging.
For example, P20 steel nitrided at a temperature of 510°C for 80 hours, with an ammonia dissociation rate of 30-40%, results in a nitriding depth of 0.3-0.5 mm and a surface hardness of 650-700 HV.
In contrast, H13 steel, after quenching and two rounds of tempering followed by surface nitriding, can achieve surface hardness around 1000 HV with a nitriding layer depth of approximately 0.24 mm. However, this high hardness is more commonly used for aluminum extrusion molds and is less frequently applied to injection molds.
Conclusion
In conclusion, selecting the right mold steel type is crucial for ensuring high-quality, durable, and cost-effective production in the plastic injection molding industry. Understanding the characteristics, applications, and common types of mold steel allows manufacturers to make informed decisions that suit their specific needs and enhance overall production efficiency.
As technology evolves, so does the range of available mold steels, promising even greater precision and durability for future manufacturing challenges.