For many individuals, the term “all-electric injection molding machine” might be relatively unknown or perceived as a complex, high-end technology. However, this technology, which originated in the 1980s, experienced significant advancements in the 1990s.
It’s essential for users to grasp what these machines are and the appropriate scenarios for their use. This article aims to explain these aspects in an uncomplicated and precise manner.
What is an all-electric injection molding machine?

All-electric injection molding machines represent a significant innovation in the field of injection molding, distinguished by their use of electric servo motors to control all operational movements. This is a departure from traditional hydraulic injection molding machines, which rely on hydraulic systems to perform key functions such as mold opening and closing, plastic injection, and product ejection.
In all-electric machines, servo motors replace these hydraulic systems. This change brings about notable benefits, including enhanced precision and speed in each action. Additionally, the integration of pressure and temperature sensors facilitates closed-loop control, significantly elevating manufacturing accuracy.
These machines are especially beneficial in sectors where high precision and consistent replication are critical, such as in the production of medical devices and precision electronics. Overall, all-electric injection molding machines signify a progressive step in injection molding technology, embodying efficiency, precision, and environmental sustainability.

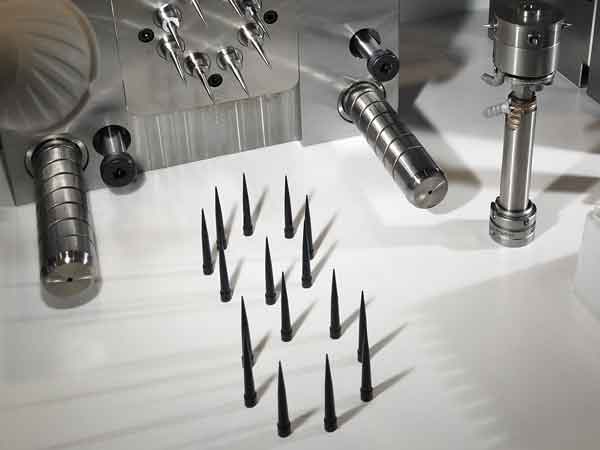
The Benefits of All-Electric Injection Molding Machines
All-electric injection molding machines bring a plethora of advantages to the manufacturing process, including:
1. Higher injection Speed and Pressure
- All-electric injection molding machines typically reach pressures of 300-400Mpa, significantly surpassing the 120-150Mpa of hydraulic machines.
- For injection speed, electric machines can achieve 300-1000mm/s, while hydraulic machines hover around 100mm/s, with high-speed hydraulic models reaching 150-200mm/s.
2. Enhanced Manufacturing Accuracy:
- Utilizing servo motors for driving various components, these machines offer more precise control. This results in improved quality and consistency in the final products.
- Many all-electric models boast a weight accuracy of ±0.3-0.5%, with some even achieving ±0.1%. In contrast, hydraulic machines typically offer weight accuracy above 1%.
- In terms of dimensional accuracy, all-electric machines are often advertised to achieve within 0.01mm, significantly surpassing the 0.1-0.2mm accuracy of hydraulic machines.
3. Superior Energy Efficiency:
Servo motors make these machines more energy-efficient compared to traditional hydraulic counterparts. They consume energy only when necessary, leading to electricity savings of 40-60%.
4. Lower Lubrication and Noise Levels:
- The electric drive nature of these machines means they require less lubrication than hydraulic ones and operate with considerably less noise.
5. Precise Control and Quick Response:
- All-electric machines allow for finer control over injection speed and pressure. They also respond faster, enhancing productivity.
- For instance, consider a headphone stand made of ABS, with 16 mold cavities. While a hydraulic machine might take 24 seconds to mold it, an all-electric machine can accomplish this in just 18 seconds, significantly cutting down time.
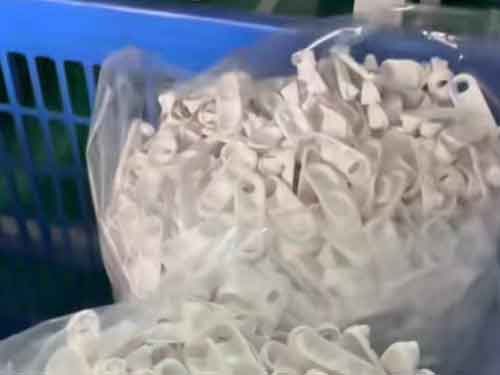
Overall, the shift to all-electric injection molding machines represents a significant leap in manufacturing efficiency and precision, aligning with modern demands for high-quality, cost-effective, and environmentally friendly production.

Comparison table of the key features
Below is a comparison chart that outlines the main differences between traditional hydraulic injection molding machines and all-electric injection molding machines, focusing on their essential characteristics.
Feature | Traditional Hydraulic Injection Molding Machine | All-Electric Injection Molding Machine |
---|---|---|
Weight Accuracy of Molded Products | Generally above +/-1% | Many can achieve +/-0.3 to 0.5%, some can reach +/-0.1% |
Positioning Accuracy | Controlled by electronic ruler, generally at 0.3mm, high-speed precision machines can reach 0.2mm | Servo motor full-closed loop control with high-precision encoders, positioning accuracy can be controlled within 0.1mm |
Minimum Injection Speed | Struggling with very low injection speeds, which restricts the manufacturing of extremely small products. | High positioning accuracy allows for very low injection speeds |
Maximum Injection Speed | Generally around 100mm/s, some high-speed injection molding machines can reach 150-200mm/s | Generally can reach 300-1000mm/s |
Maximum Injection Pressure | Ordinary injection molding machines can reach 120-150Mpa | Generally can reach 300-400MPa |
The Drawbacks of All-Electric Injection Molding Machines
Despite their numerous benefits, all-electric injection molding machines also present certain challenges and limitations, including:
Higher Initial Costs:
- The upfront cost of an all-electric injection molding machine is typically higher than a traditional hydraulic counterpart. This is largely due to the expensive high-precision servo motors and sophisticated control systems they utilize.
- In China, for example, the price of a new hydraulic machine is often on par with that of a second-hand all-electric machine. Furthermore, imported all-electric machines can cost about 2-4 times more than those manufactured domestically. Consequently, using an all-electric machine for production usually incurs a higher hourly rate.
Clamping Force Limitations:
- For extremely large parts, all-electric machines may not be as effective as hydraulic presses, which generally offer greater advantages in terms of handling large sizes and exerting high clamping forces.
Maintenance and Technical Expertise:
- Maintaining all-electric machines can require more specialized technical knowledge due to their complex electronic control systems. The maintenance and troubleshooting processes can be more intricate compared to hydraulic presses.
- Moreover, due to sensitive components like ball screws, all-electric machines are less tolerant of wear and tear on parts.

4. Electricity Dependence:
- While all-electric machines are typically more energy-efficient than hydraulic ones, their reliance on a consistent and stable power supply is a notable drawback. In regions with fluctuating or unreliable electricity, this dependency can pose significant challenges.
Understanding these drawbacks is crucial for manufacturers considering an investment in all-electric injection molding machines, ensuring a balanced assessment of their potential in various production environments.
Prominent Brands in All-Electric Injection Molding Machines
The realm of all-electric injection molding machines is marked by the presence of both prominent domestic and global manufacturers, each bringing their own expertise and innovations to the field.
Notable Domestic (Chinese) Brands:
- LKIMM / 力劲: A key player in the Chinese market, known for their advanced technology in all-electric machines.
- Haitian / 海天: One of China’s largest manufacturers, Haitian is renowned for its efficient and reliable machinery.
- Yizumi / 伊之密: Yizumi stands out for its innovative solutions and has made significant strides in the all-electric segment.
- Chen Hsong / 震雄 Chenhsong: With a long history in the industry, Chen Hsong is recognized for its durable and precise machines.
- Welltec / 东华: Welltec has carved a niche for itself with its high-performance all-electric injection molding machines.
Internationally Acclaimed Manufacturers:
- Sumitomo: A Japanese giant, Sumitomo is celebrated for its precision and cutting-edge technology in all-electric injection molding.
- Toshiba Machine: Toshiba Machine is another Japanese leader known for its robust and efficient all-electric machines.
- FANUC: FANUC, also from Japan, has a reputation for highly automated and innovative all-electric injection molding solutions.
- Sodick: Specializing in precision molding, Sodick offers advanced all-electric injection molding machines.
- Arburg: Based in Germany, Arburg is a key figure in the European market, renowned for its high-quality all-electric machines.
- KraussMaffei: Another German powerhouse, KraussMaffei is known for its sophisticated and versatile machinery.
- Battenfeld: A part of the Wittmann Group, Battenfeld has a strong presence in the global market with its efficient all-electric machines.
These brands, with their diverse range of all-electric injection molding machines, cater to various industrial needs, emphasizing innovation, efficiency, and precision. Their contributions significantly shape the landscape of modern manufacturing technology.

Summary
In conclusion, the journey into the world of all-electric injection molding machines reveals a landscape rich in innovation and efficiency. These machines offer a multitude of advantages, including precision, energy efficiency, and environmental friendliness, making them an increasingly popular choice in various manufacturing sectors.
However, it’s essential to weigh these benefits against their higher costs, technical requirements, and certain operational limitations. Understanding the offerings of leading brands, both domestic and international, can further guide decision-makers in choosing the right equipment for their specific production needs.
As technology continues to evolve, all-electric injection molding machines stand as a testament to the industry’s commitment to progress, precision, and sustainability.