What is Conformal Cooling?
Conformal cooling is an innovative application of 3D printing technology in the field of mold design and manufacturing. The characteristics of this technology lies in the use of 3D metal printing to create internal channels that perfectly match the shape of the product. Such cooling channels are designed to closely follow the contours of the product, enabling rapid and uniform cooling inside the mold.
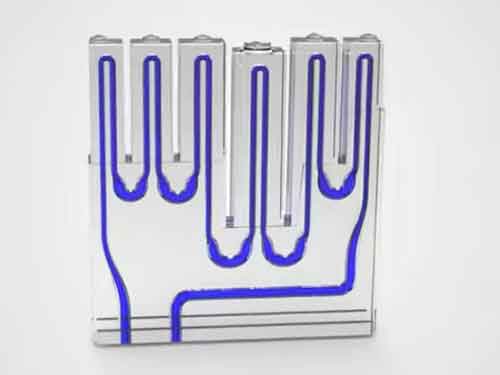
Compared to traditional linear cooling channels, conformal cooling technology is far more efficient, significantly enhancing the quality and efficiency of mold manufacturing. In essence, this technology revolutionizes the cooling process in mold design, making it more precise and effective – a significant advancement in the field.
The Importance of Temperature of Injection Mold
In the process of using injection molds, temperature control plays a crucial role in ensuring the quality of plastic products and improving production efficiency. The temperature of the mold directly affects the flow of the plastic, the surface quality of the product, and the distribution of internal stresses within the product.
When the temperature of the mold is too low, it can affect the flowability of the plastic and surface smoothness. Additionally, a lower mold temperature may increase internal stresses in the product, reducing its strength and stability.
Conversely, if the mold temperature is too high, it extends the cooling time of the plastic within the mold. This not only prolongs the production cycle but can also lead to uneven cooling of the product, resulting in deformation or warping.
Therefore, in the injection molding process, it is vital to appropriately heat or cool the mold based on the properties of the plastic used and the requirements of the product. In most cases, cooling the mold is necessary to ensure rapid solidification of the plastic, enhance production efficiency, and guarantee the quality and dimensional accuracy of the product. Proper temperature control is one of the key factors in achieving efficient and high-quality injection molding production.
Limitations of Traditional Methods in Cooling Channel Machining
In traditional mold manufacturing methods, cooling channels are typically created using milling machines or deep-hole drilling. The main limitation of this approach is the technological constraint that results in most channels being straight. Such straight cooling channels cannot fully adapt to the complex geometrical shapes of molds, especially in the taller and narrower sections of the mold, making it challenging to achieve effective cooling channel layouts.
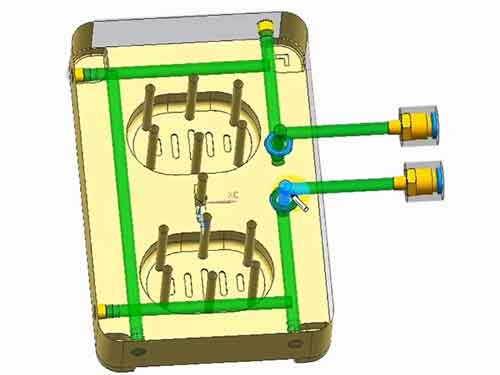
This limitation of straight channels often leads to uneven cooling and reduced cooling efficiency during the use of the mold. This uneven cooling can directly affect the quality of plastic products, potentially causing issues like warping, excessive internal stress, or inaccurate dimensions.
Moreover, the traditional design of straight cooling channels limits the optimization potential of the mold cooling system. The inability to precisely control cooling effects often hinders the maximization of production efficiency and may lead to increased energy consumption.
Therefore, in modern mold design and manufacturing, finding new technologies to overcome these limitations, such as 3D-printed conformal cooling channels, has become an important trend in the industry. These new technologies allow for more flexible waterway designs that better adapt to the geometrical shapes of molds, thereby achieving more uniform and efficient cooling effects.
Superiority of Modern 3D Metal Printing
Modern 3D metal printing technology has shown significant advantages in the field of mold manufacturing. This technology, which builds objects layer by layer through additive manufacturing, greatly expands the possibilities for internal channel design.
Compared to traditional milling or drilling methods, 3D printing faces almost no limitations in terms of shapes. It can create complex internal structures, which are crucial for enhancing the cooling efficiency of molds and the quality of the final products. This ability to intricately design and manufacture cooling channels that conform precisely to the mold’s geometry not only optimizes the cooling process but also opens up new avenues for innovation in mold design.
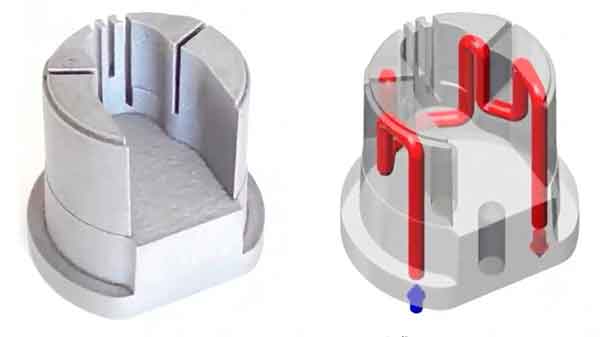
Common Technologies and Materials
The technology commonly used for producing conformal cooling mold parts today is Selective Laser Melting (SLM). This technique is relatively mature and cost-effective.
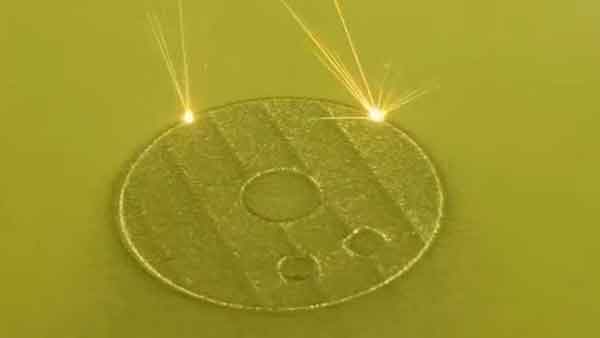
Common materials
Regarding the metal materials used for printing, these materials now can compete with traditional mold steels in terms of performance. Commonly used materials include 1.2709, CK (or Corrax), and MAMS (equivalent to SKD61). Taking 1.2709 mold steel as an example, it has several significant advantages:
High Density: The density of 1.2709 can reach up to 99.9% with very few pores. This means that the printed parts can withstand higher working pressures and more severe working environments. Furthermore, the material can be polished to A2-A1 levels, eliminating concerns about internal pores.
High Hardness: After heat treatment, the hardness of 1.2709 can reach HRC48-52. Such high hardness provides the mold with better wear resistance and durability, making it particularly suitable for long-term or high-intensity production environments.
Good Thermal Conductivity: The thermal conductivity of 1.2709 is similar to traditional mold steels, which is crucial for ensuring uniform and efficient mold cooling.
Ease of Post-Processing: Although 1.2709 is manufactured through 3D printing, it can still be machined, EDM’d, and polished through conventional methods to achieve high-quality mold surface standards.
In summary, modern 3D metal printing technology not only offers significant advantages in design flexibility but also matches traditional mold manufacturing methods in material performance, bringing a revolutionary change to the mold manufacturing field.
Advantages of Conformal Cooling
More Uniform Cooling: Since the cooling channels are closer to the mold surface and follow the shape of the product, a more uniform cooling effect is achieved. This helps reduce stress, deformation, and uneven shrinkage in the product.
Increased Production Efficiency: Uniform cooling can shorten cycle times, thereby improving production efficiency.
Enhanced Product Quality: Even cooling contributes to improved dimensional accuracy and surface quality of the product.
Energy Saving: Shorter cooling times mean the overall production process is more energy-efficient.
These advantages highlight how conformal cooling technology optimizes the molding process, leading to better product outcomes and more efficient manufacturing practices.
Limitations of Conformal Cooling
High Cost: Conformal cooling often relies on 3D printing technology for manufacturing, and the cost of 3D printing equipment and materials is relatively high. This results in higher initial investment and manufacturing costs for conformal cooling systems compared to traditional cooling systems.
Complexity in Design and Manufacturing: Designing conformal cooling channels requires specialized software and a high level of design expertise. The manufacturing process is also relatively complex, necessitating precise control and professional operation.
Size Limitations: Due to constraints related to the size of the printing bed and costs, this technology is currently more suited for smaller molds or for using mold inserts, rather than manufacturing the entire lower mold through 3D printing.
These limitations underscore the need for careful consideration when deciding to implement conformal cooling technology, balancing its advantages against the higher costs and technical requirements involved.
Embracing the Future of Mold Manufacturing
In conclusion, while conformal cooling represents a significant advancement in mold manufacturing, offering uniform cooling, enhanced product quality, increased efficiency, and energy savings, it is not without its challenges. The high costs, complexity in design and manufacturing, and size limitations are factors that must be weighed carefully.
As technology continues to evolve, and with further advancements in 3D printing, it is likely that the accessibility and applicability of conformal cooling will expand, making it a more viable option for a wider range of manufacturing needs. Embracing these innovative technologies is key to staying competitive and efficient in the dynamic field of mold manufacturing. As we move forward, it’s exciting to think about the potential transformations and improvements that conformal cooling and related technologies will bring to the industry.
Comments are closed.