Finding a qualified mold manufacturer in China is challenging but there are strategies.
Over the past few decades, China’s mold manufacturing industry has developed a comprehensive and rich industrial chain, attracting global customers with its highly competitive pricing. However, finding a qualified and reliable plastic mold manufacturer in this opportunity-rich market is a daunting task. It requires not only verifying their technical knowledge and experience but also assessing their honesty, integrity, and adherence to business ethics. Language and cultural differences add another layer of complexity to this challenge.
Nevertheless, with the right evaluation methods and sufficient effort, it is possible to discern the quality of a manufacturer. A key approach is to engage in in-depth technical discussions early on. This not only tests their technical prowess but also allows observation of their attention to detail and patience in communication. Generally, individuals who can engage deeply on technical topics tend to be reliable in character; conversely, those lacking in integrity often show impatience in communication and lack depth in technical discussions.
This article will further discuss how to evaluate a mold manufacturer from two aspects: assessing their technical capabilities and judging their business ethics. These are crucial for identifying a qualified mold manufacturer.

What pitfalls you need to avoid
Firstly, it’s essential to understand the problems that can arise from working with unqualified mold manufacturers. This understanding is crucial when evaluating suppliers. Despite the abundance of mold factories, after filtering through criteria such as price, technical capability, and service attitude, only about 5% of them might be suitable for your needs.
The main issues to avoid include:
- Injection Molding Product Quality Issues
- These encompass molding defects like flash, weld lines, and inconsistencies in surface color and glossiness.
- Additionally, inadequate dimensional accuracy can result in products having loose connections or failing to function properly.
2. Mold Quality Issues
- Issues such as poorly designed gates and ejection mechanisms can make molds barely usable, and redesigning them may necessitate starting from scratch—a cost most mold factories are unwilling to bear.
- Moreover, not using high-precision equipment for mold making can lead to fitment issues and accelerated wear and tear, reducing the mold’s lifespan.
3. Delivery Delays
- Manufacturers not meeting the agreed-upon timelines, especially taking longer than expected to make modifications after the T0 sample has been produced.
4. Integrity Issues
- Some manufacturers cut corners by not using the agreed-upon mold materials and processing equipment, which is a severe issue. Honesty is the foundation of all cooperation. You should do your utmost to avoid people who make many promises in person but fail to follow through afterwards.
For instance, we once worked with a new mold factory that did not follow through with the agreed-upon mirror spark erosion and high-speed milling, leading to excessive manual polishing and uneven surfaces on the mold. Subsequent litigation recovered the mold down payment, but it resulted in significant time and financial losses.
The part on the right was made by that mold factory, and it differs significantly from the original sample we provided them.
The one on the left was made later by another mold factory, it basically meets the quality standards.
5. Language and Cultural Barriers
- Many Chinese mold manufacturers employ salespeople to communicate with clients, but their English proficiency is often limited, and their understanding of mold technology is not particularly deep, which can increase the difficulty and cost of communication. However, with the advent of AI, this issue has seen some improvement.
- At the same time, cultural differences lead to deviations in understanding matters, causing communication to be less smooth, and discrepancies between expectations and reality can also be quite frustrating.
Understanding the Characteristics of Injection Mold Workers
Injection mold workers possess distinctive characteristics, and recognizing these can help in interacting with them more effectively.
Skilled Craftsmanship
A mold worker is a skilled artisan proficient in producing and assembling injection molds. To become qualified, a mold worker typically undergoes 2 to 3 years of training to master various skills, including metalworking, heat treatment, using CAD software, fitting skills, understanding mold structures, and troubleshooting, among others.
Educational Background
In China and most parts of the world, mold makers often do not need a college degree. A high school diploma is the most common educational attainment among them. However, some pursue associate’s or bachelor’s degrees in related fields. Many also complete apprenticeships, lasting anywhere from 2 to 4 years, to acquire practical experience and knowledge.
Challenging Working Conditions
Mold makers work in conditions that can be tough: environments that are noisy, dirty, and greasy, with high temperatures and potential for injuries. Their work often demands long hours to fulfill deadlines and meet customer expectations.
Despite the profession’s demands and varying levels of skill among workers, the working conditions and compensation for mold makers might not attract those with the highest academic achievements.
Unlike office workers who might be more adept at mastering office software, organizing tasks, and managing time efficiently, mold workers might lag in these areas due to the nature of their work. Mold making is a demanding profession, requiring a different set of skills and tolerances than those found in office environments.
Large mold companies vs. small mold shops

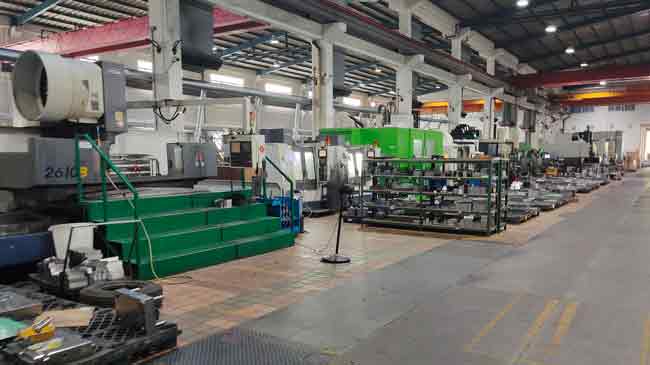
When you first approach an injection mold factory, it’s crucial to understand the size of the company. Companies of different sizes offer distinct differences in pricing, service, and quality. Depending on the scale of your project, finding a company of the appropriate size to collaborate with is essential. The table below provides an overview of the differences between large mold companies and small mold shops.
Small-sized | Medium-sized | Large-sized | |
---|---|---|---|
Number of employees | 1-10 | 10-100 | 100-1000 |
Machining equipment | Mostly outsourced | Some outsourced, some in-door | Mostly in-door, some outsourced |
CAD design ability | Mostly outsourced, Some can do CAD design on their own | Some have an internal designer team of 2-3 people | Some may have an internal designer team of 20-30 people |
Expertise on mold making | Uncertain | Uncertain | High |
Their attention on your project | High | Uncertain | Moderate |
Trustworthy on Quality and on-time delivery | Uncertain | Uncertain | High |
Mold price | 1x | 1.5-2.0x | 2.5-3.0x |
Here are some more notes:
Employee Numbers and Their Impact
Small Mold Factories:
- Employee Count: Typically have a lean team without redundant staff, which helps in cost-saving but could lead to potential staff shortages.
- Client Interaction: Often lacks a dedicated office clerk for customer interactions, meaning the factory owner frequently handles project communications directly. This can facilitate effective communication due to direct involvement in the project.
Medium-Sized Mold Factories:
- Employee Structure: Possess a larger number of employees compared to small factories. Mold makers generally work independently.
- Client Communication: Features an office clerk to manage communications with clients. However, this clerk may not possess deep knowledge about molds, which can occasionally lead to communication barriers with the molders. There’s also a risk of variable work quality as the skill level of the mold maker assigned to your project may vary.
Large Mold Factories:
- Organizational Structure: Boast a well-organized company setup with ample staffing to cover all necessary roles.
- Project Management and Quality: Typically have dedicated teams that focus on technical solutions, material sourcing, and quality inspections, enhancing the likelihood of project success and timely delivery.
Quality Systems and Mold Making Expertise
Large Mold Factories:
- Skills and Expertise: Generally possess superior mold-making skills and expertise.
- Quality Systems: Often have formal quality systems like ISO 9001 in place. However, to save time and effort, they might not strictly follow every step for each pair of molds, and they tend to produce less paperwork per project.
Medium-Sized Mold Factories:
- Quality Claims vs. Reality: Many claim to follow quality systems like ISO 9001, but implementation may fall short in practice.
- Work Style: Mold makers often work independently, with less supervision or guidance, which doesn’t guarantee superior quality over smaller factories.
Small Mold Factories:
- Management Flexibility: Offer more flexibility in management but might lack organizational structure.
- Talent Over System: Despite potential disorganization, individual molders can be highly skilled. Evaluating these factories often focuses more on assessing individual talents rather than the factory’s systemic qualities. Direct communication with molders can help circumvent some issues typically caused by middlemen or coordinators.
Their attention on your projects
Small mold factories are likely to pay more attention to your project as you are a big customer for them.
Medium-sized mold factories often depend on 2 or 3 large customers to sustain them, so you may not be a priority. And their company is more influenced by a few key people, and you need their support.
For large mold factories, because they have a dedicated coordinator or project manager for your project, they can provide a certain level of attention to small and medium-sized customers too.
Generally, small mold factories will probably give you more attention and cooperation in solving complex problems.
Baseline Quote for Comparison: Assuming a small mold factory’s quote for a mold is $10,000, this serves as our comparison benchmark.
- Small Mold Factories: Known for the lowest prices, leveraging minimal operating costs to offer molds at a baseline of $10,000.
- Medium-Sized Makers: Their mold prices vary between $15,000 and $20,000, a reflection of their moderate operational costs and level of prifit expectation.
- Large Mold Companies: These entities set their prices in the range of $20,000 to $25,000, attributed to their comprehensive resources and superior quality systems.
This concise summary delineates the impact of factory size on mold pricing, illustrating the spectrum from cost-effective options provided by small factories to the premium offerings of large companies.
5 aspects to examine and select plastic mold manufacturers
After understanding the information above, we now arrive at the focal point of this article, where we will introduce the criteria we use to evaluate plastic mold manufacturers.
1. Get to know their business background, location and price
The first thing we need to know is the size of their company, and whether their offer is in line with the size of their company. If the price is not right, then there will be no point in continuing the communication.
Tip:
You may want to request the mold makers to provide the cost breakdown, so you can compare them and see if each cost is accurate and reasonable. However, the large companies may refuse to do this because it may expose their high overhead and make them look bad.
You can use our online mold cost calculator to get an estimate of the reasonable cost for each item and the total price. This is only for reference, as different molds may have some variations in designs.
It is also important to know where the company is located, whether it is in an area where the mold industry is well-developed. This is because these areas have more people and equipment for design, processing, and so on, and are more likely to produce better mold companies. For example, Dongguan and Shenzhen in Guangdong, Ningbo in Zhejiang, and Kunshan in Jiangsu.
We also have a map of mold companies that shows our trust level, some cities we are reluctant to approach because we have bad experiences in the past, before understanding that some places have different folkways. Of course, this is not a fixed rule.
2. Test them with a difficult part
What this mean is not to use the parts you want to make to let them quote, but to use a product with a higher difficulty to let them quote.
The logic behind this is that it is very difficult to judge the skill or talent of a mold maker by the usual difficulty of the product, but why does this matter?
Well, if you only let them to do occasional small batches of simple products, this may not be a big deal. But if you want them to do large batches of simple products, or if you plan to work with them for a long time to develop more products, this will be more important.
Also, and this may be a bit of a personal bias, I think there is a correlation between the level of knowledge and the level of integrity of a mold maker.
3. Ask them to provide quality inspection report
See if the factory can provide inspection reports and correction plans for T0 samples (or even T1, T2 samples, etc.)
Generally, such inspection reports cover injection molding defects (e.g. flashes, warpage, weld line lines, etc.), whether key dimensions are within tolerance, and the appearance of the product (uniformity of surface texture, color, etc.).
This is because factories need to be in the habit of inspecting their own products, rather than relying on customers to do so. This will save you a lot of time and effort. But if you have to make trade-offs, this point is less important, because the small factories may be aware of the issues but do not have time to complete the report.
4. Ask them to deliver a DFM report
The DFM report can provide the basic design of the mold (e.g. gate type/location, ejector pin location, etc.) which will have a direct impact on the quality of the product.


The DFM report also provides a wall thickness/draft analysis, and suggests changes to the product design.
In addition, the DFM report will also include what injection molding defects are likely to occur in the product, and take countermeasures to reduce the extent of injection molding defects.
There are many small and medium-sized molders who do not know how to produce a DFM report, but it is important for future product quality assurance.
You may not need the DFM report for simple plastic parts, but it is beneficial to know that the factory has this capability.
5. Are they courteous and responsive?
You want to feel that they are interested in your project, that they understand your needs and expectations, and that they are willing to communicate with you throughout the process. That is why it is important that they are courteous and responsive when you contact them.
They listen to your questions and concerns, and answer them clearly and honestly. They show that they value your time and business, and that they care about your satisfaction.
They reply to your messages or calls as soon as possible, preferably within 24 hours. They provide you with the information or documents that you request, such as quotes, samples, or references. They update you on the progress of your project regularly, and inform you of any changes or issues that may arise. They follow up with you after the completion of your project, and ask for your feedback or suggestions.
Being courteous and responsive when contacting a mold maker can help you establish a good rapport and trust with them. It can also help you avoid misunderstandings, delays, or disputes that may affect the quality or delivery of your project. It can also increase your chances of having a successful and long-term partnership with them.
Have a reasonable expectation for a Chinese mold maker
When seeking a Chinese mold maker, particularly if you’re not a major customer, finding one that meets all criteria can be challenging. Should compromises be necessary, the importance of various aspects can be ranked as follows:
Item | Level of importance |
Business background, location and price | High |
Test them with a difficult part | Medium |
Ask them to provide quality inspection report | Low |
Ask them to deliver a DFM report | High |
Are they courteous and responsive | High |
This organized approach helps set realistic expectations when selecting a Chinese mold maker, prioritizing key factors for a successful partnership.
Tips for Ensuring Quality and Delivery of Your Mold Project
When you are making the mold, you need to follow some steps to ensure the quality and delivery of your project.
First, you need to ask for a timetable from the mold maker before they start working on your mold. The timetable should include the milestones, deadlines, and deliverables of each stage of the mold-making process. If possible, you should also sign a contract with the mold maker that specifies the terms and conditions of your cooperation.
Second, you need to contact the mold maker regularly to ask for updates on their progress. You should also check if they are following the timetable and meeting the quality standards. If there are any changes or delays in the timetable, you should ask for the reasons and request a revised timetable.
Third, you should not be afraid to be persistent and assertive when contacting the mold maker. You are not being annoying, but rather showing your interest and involvement in your project. You need to do this from time to time to make sure that your project is done on time and according to your expectations.
(This post was originally written in Jan. 2020 and revised in Jun. 2023)

Comments are closed.