At Boyan, we occasionally delve into rapid prototyping, although it’s not our core business. We have regular partners handling this aspect, saving our clients time in finding suitable 3D printing suppliers and ensuring faster, more reliable service.
the Role of 3D Printing service at Boyan
The main purposes of 3D printing in our context include:
1. Design Verification and Functionality Confirmation:
Before starting mold production, we use 3D printing to confirm that the design is error-free and meets expected functional requirements. This forms the majority of our 3D printing work, mainly serving as a final check before mold fabrication begins.
Example 1
This is a plastic connector we designed for joining two aluminum profiles. It incorporates a snap-fit mechanism, which means it will undergo significant compressive force during assembly. Therefore, we chose to print this sample using nylon material due to its higher strength compared to other plastics.
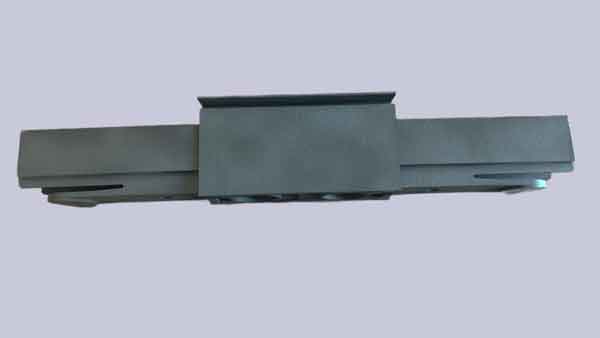
However, the snap-fit’s resilience is somewhat less than that of genuine nylon. Nonetheless, it still meets our expectations and requirements.
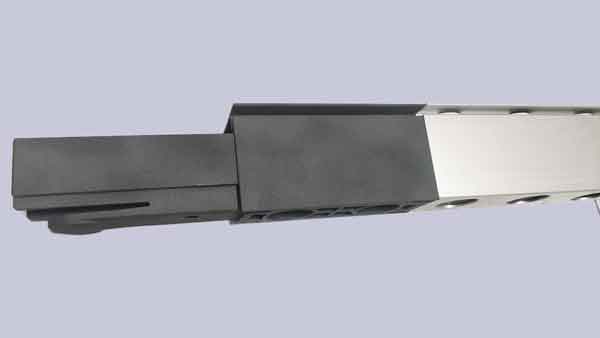
Example 2
In this example, we can assemble the various components together and test the fit for tightness or looseness, as well as ensure the snap-fit functions as anticipated.
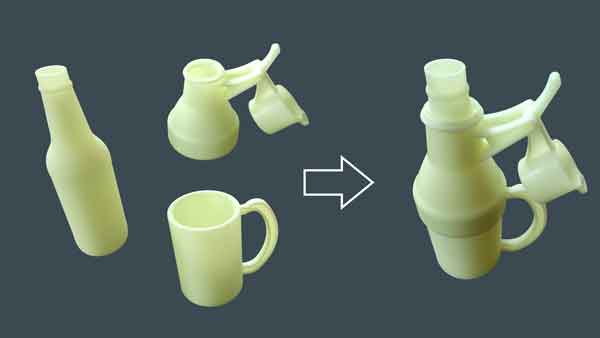
2. Presentation Prototypes:
We use 3D-printed prototypes for internal and external demonstrations to further explore potential improvements or assess whether to continue or terminate a project. Post-printing, the continuation of the project remains uncertain.
3. Small Batch Production:
Typically ranging from 50 to 150 pieces, this approach tests market receptivity while saving on mold costs. It’s crucial to evaluate whether the investment is cost-effective, as it can rival the cost of mold production. The key difference lies in the significantly shorter production cycle. Additionally, the choice of material—taking into account mechanical properties and lifespan—is vital. While standard photopolymer resin may not always be suitable, materials like Nylon are more common, although they are limited in variety and higher in cost.
4. Utilization as Inspection Tools:
Products printed with photopolymer resin can achieve an accuracy of +/- 0.1~0.2mm, making them suitable for use as inspection jigs. This approach allows for the verification of complex three-dimensional surfaces against initial designs. Furthermore, the cost of 3D printing these tools is significantly lower than CNC machining. This means they can be effectively used as inspection tools with slightly less precision and shorter lifespan, but at a much lower cost.
Example 3
In this example, we utilize a 3D printed sample to verify if the three-dimensional contour of the injection-molded parts matches the intended design curvature. We first need to design the shape of this inspection jig, which is reverse-engineered based on the product’s 3D curved surface.
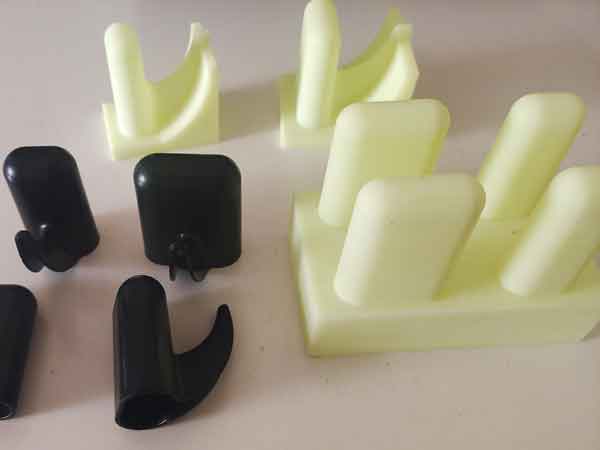
After the plastic product is produced, we fit it onto the jig, using our hands to gauge the snugness of the fit and visually inspecting to ensure the contour aligns perfectly.
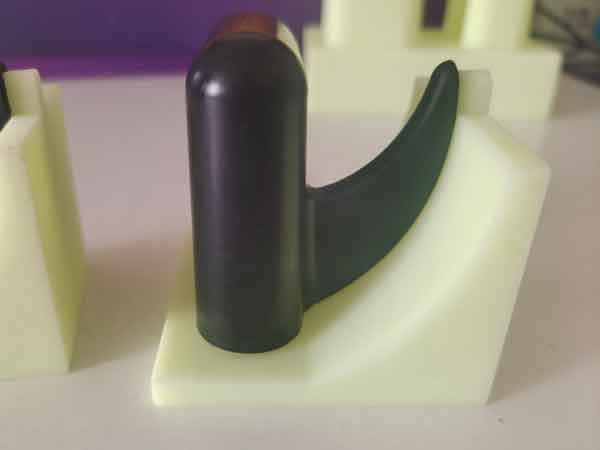
In summary, 3D printing plays a versatile role in rapid prototyping, from design verification to market testing. Through collaboration with our professional partners, we offer comprehensive and efficient 3D printing solutions to our clients.
5. Support structures for correcting deformations:
Plastic products can sometimes deform or warp. A common solution is to use support structures inside the product immediately after injection molding to counteract the deformation. Once the supports are removed, the product can achieve a smooth state.
These support structures need to be designed with a three-dimensional curved shape to fit the product’s sidewalls well, avoiding localized point contacts that could leave marks. Conventional CNC machining methods for such designs would be costly, but utilizing 3D printing significantly reduces the cost.
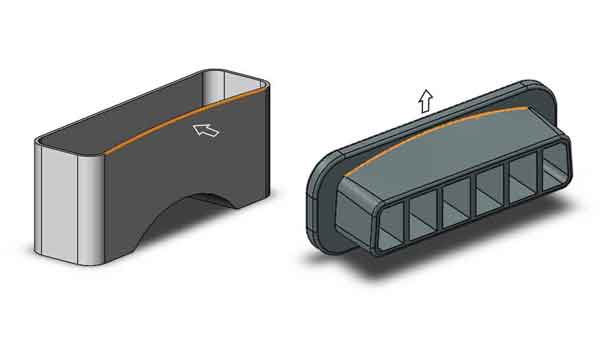
Example 4
For instance, in the plastic product depicted below, one side’s sidewall caves in after injection molding, while the other side remains flat. Considering this, we have designed a support structure to effectively shape the product.
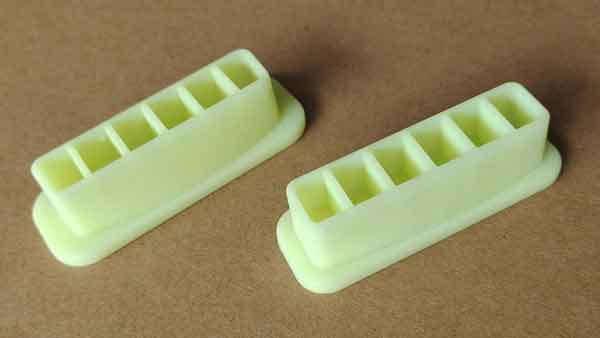
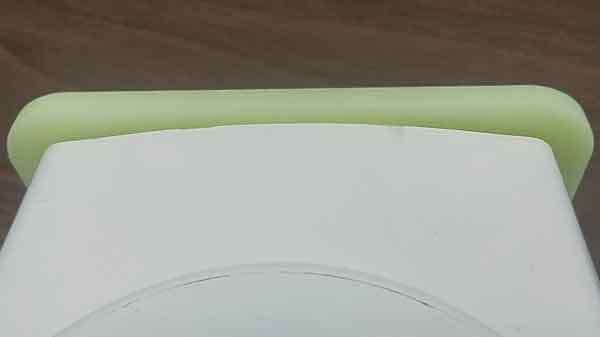
The materials we use for 3d printing
In reality, while there are numerous materials available for rapid prototyping and 3D printing, many of them are either not widely adopted or quite expensive. Therefore, considering cost and availability, we currently use only the following four types of materials:
1. Photopolymer Resin: This is a widely used 3D printing material, favored for its balanced overall performance. Parts printed with photopolymer resin have a smooth surface, decent strength, and moderate heat resistance, all at a relatively low cost. However, it has its drawbacks: it may not be strong enough under sustained load, can deform under prolonged stress, and might discolor over time.
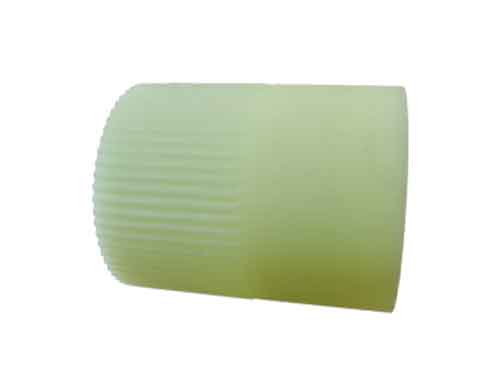
2. Nylon: Known for its higher strength, reportedly reaching 60-80% of that of injection-molded nylon. However, the actual strength can vary depending on each factory’s conditions, such as the equipment used, production materials, and manufacturing processes. Nylon has a noticeably textured surface with visible grains and lines, and it is also somewhat more expensive.
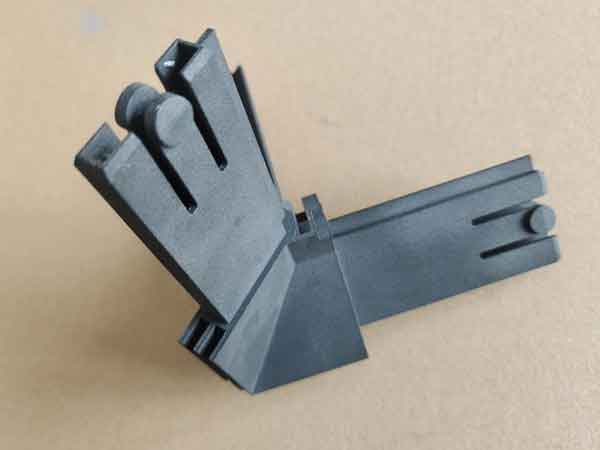
3. PMMA (Acrylic): Mainly used for parts requiring transparency. However, its transparency is not as high as that of injection-molded transparent parts, with some surface unevenness and a matte appearance.
4. Silicone, TPU, and Other Soft Rubber Materials: These materials are very practical, providing rapid prototyping solutions for soft rubber products. They emulate the properties of traditional soft rubber materials to a certain extent and are suitable for applications that require softness and elasticity.
Overall, our selection of 3D printing materials aims to balance performance, cost, and versatility in application. By carefully choosing materials suitable for specific needs, we can effectively meet our clients’ demands in rapid prototyping and small-batch production.
A Comprehensive Table of Rapid Prototyping Technologies and Materials
With the rapid advancement of prototyping technologies (including 3D printing and others) and the ever-increasing variety of materials available, it’s often not necessary to have an in-depth understanding of each one. A general knowledge is usually sufficient.
To provide a more concise and clear reference, we have compiled a table that lists the common rapid prototyping processes available in the market today, along with their corresponding materials and the forms of these materials. This way, our clients and partners can quickly access essential information and make more effective decisions tailored to their specific needs.
Rapid Prototyping Technology | Corresponding Materials (Plastics Only) | Form of Material |
---|---|---|
Fused Deposition Modeling (FDM) | PLA, ABS, PETG, TPU, etc. | Filament |
Stereolithography (SLA) | Photopolymer Resin | Liquid Resin |
Selective Laser Sintering (SLS) | Nylon, Polystyrene | Powder |
Digital Light Processing (DLP) | Photopolymer Resin | Liquid Resin |
Fused Deposition Modeling (FDM) | PLA, ABS, PETG, TPU, etc. | Filament |
PolyJet Printing | Various Photopolymer Resins (flexible, rigid) | Liquid Resin |
Powder Bed and Inkjet Head 3D Printing | Metal Powder, Plastic Powder (including PMMA), Ceramic Powder | Powder |
Binder Jetting (for plastics) | Acrylic, Nylon | Powder |
CNC Machining (for prototyping) | ABS, Polycarbonate, Acrylic, Nylon | Solid Block |
Vacuum Casting | Polyurethane Resin (mimicking various plastics) | Liquid Resin |
Summary
In summary, while rapid prototyping isn’t our primary business, we are capable of providing these services through our trusted suppliers. This article outlined the key materials available and offered examples for quick understanding. If you require these services, please don’t hesitate to contact us.
Frequently Asked Questions
You can use STL, STEP, or X_T file formats. Some other formats can also be used, but converting them to these formats is usually safer.
Generally, it is between $0.1-0.15 per gram. The smaller the product, the higher the unit price.
There are many types of nylon for 3D printing, including those with and without fiberglass. The former is more expensive. Generally, their prices range from $0.25-0.35 per gram.
As seen from the unit prices mentioned earlier, the unit price of 3D printing is higher, but there are no initial mold investment costs. Generally, the cost of 50-100 3D prints can reach the cost of a mold. Additionally, 3D printing materials are often inferior to the plastics used in injection molding.
Samples made of photosensitive resin require 1 day, while nylon and other materials generally require 1-3 days.