Introduction to injection molding vs 3d printing : A Manufacturer's Perspective
As a manufacturer specializing in injection molding, we often receive requests for 3D printed parts. Occasionally, we also handle small-scale production of 3D printed items. But what are the pros and cons of 3D printing compared to injection molding? And when should one opt for either of these methods? This article aims to explore these questions based on our experience and knowledge.
Common Uses of 3D Printing:
There are generally two scenarios in which 3D printing is used:
1. Prototype Assembly and Design Verification: Often, we use 3D printing to produce a very small quantity, typically a single piece and sometimes up to five. The primary purpose is to assemble prototypes to check if the design is feasible or to create a demo model for presentation before the product’s official launch.
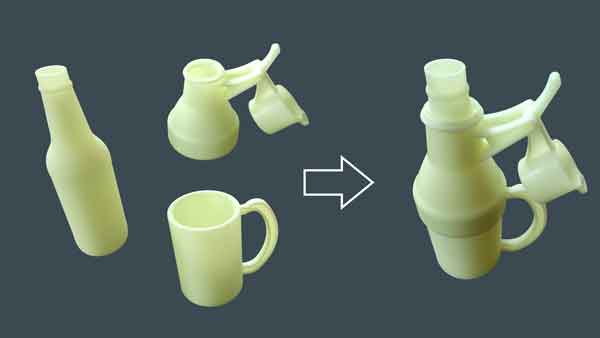
2. Small-Scale Production: This involves producing quantities ranging from 50 to 150 pieces, though such cases are relatively rare.
Opting for 3D printing in small-scale production is often motivated by the desire to avoid upfront mold costs and shorten the development cycle. But is this choice always reasonable? We believe that it’s crucial to consider the limitations of 3D printing materials in terms of performance, lifespan, and production cost. Also, the per-unit cost of 3D printing can be high. When the production volume reaches around 100 to 150 pieces, the costs start to align with those of injection molding. Additionally, there are noticeable differences in material strength, surface quality, and durability between the two methods.
Let’s analyze these aspects in detail:
Production Timeline Comparison
3D Printing: Highly Efficient
Rating: ★★★★★
3D printing is notably efficient in terms of production time. Since the equipment and materials required for 3D printing are pre-prepared and fixed, you simply need to send the 3D file to the manufacturer to initiate production. This process demands less human labor and machine setup, with most of the work being automated and carried out by the machines.
The actual printing time can take just a few hours. However, one must consider the manufacturer’s production schedule and potential delays between processes. For instance, many 3D printed parts require post-processing, such as sanding and polishing, but generally, the entire printing process can be completed within 1 to 2 days.
If shipping is required for the printed products, the total time from placing the order to receiving the samples typically takes about a week.
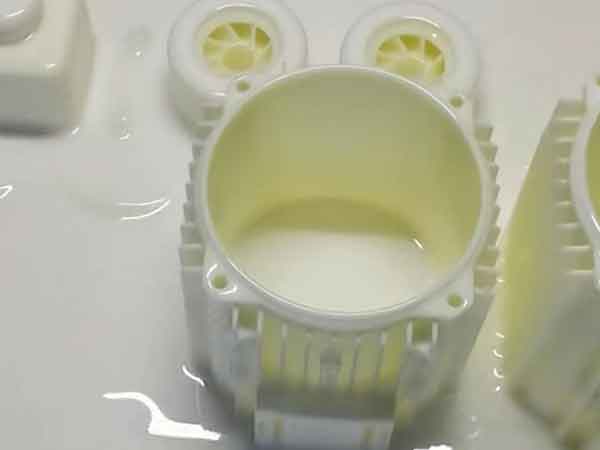
Injection Molding: Requires Patience
Rating: ★★☆☆☆
The timeline for injection molding requires much more patience. The creation of injection molds alone can take between 4 to 6 weeks. Just the design phase of the mold requires 3 to 5 days, as critical issues need to be considered and possibly revised to ensure that the mold can produce the desired quality products effectively.
Initial Investment Costs
3D Printing: Cost-Effective for Small Quantities
Rating: ★★★★☆
3D printing shines when it comes to initial investment costs, primarily because it eliminates the need for mold production. Although the unit price for 3D printing can be higher, the overall cost remains low for a few sample pieces.
There’s a wide range of materials available for 3D printing. The most common material, photopolymer resin, is relatively inexpensive. However, materials like Nylon and transparent PMMA are pricier. Using specialty materials such as stainless steel or ceramics can drive the price even higher, given their more expensive equipment and material requirements.
Injection Molding: Higher Upfront Costs
Rating: ★★☆☆☆
Injection molding requires a significant initial investment, primarily due to the high cost of mold production. Most injection molds cost between $1,000 to $5,000, leading to substantial upfront expenses.
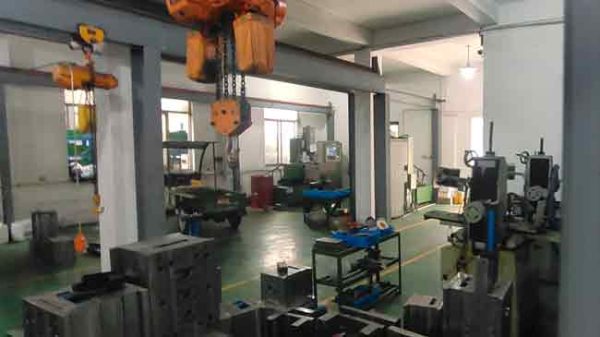
Unit Processing Time and Cost in Mass Production
Injection Molding: Ideal for Large-Scale Production
Rating: ★★★★★
Injection molding is exceptionally efficient for mass production of plastic products using molds. The cycle time for different products in injection molding can range from a few seconds to over a minute. Thanks to multi-cavity molds, the processing time per unit can be further reduced. Injection molding stands out as one of the most efficient and cost-effective methods for producing complex shapes on a large scale.
3D Printing: Less Suitable for Mass Production
Rating: ★★☆☆☆
3D printing is slower on a per-unit basis. It generally takes several hours to produce a single item. For instance, printing a simple object like a pencil holder can take over two hours. Larger parts often require 6 to 8 hours, which is quite common. Although 3D printers can be arranged to produce multiple parts simultaneously, the allocated time per individual piece is still relatively long. Consequently, the per-unit cost in 3D printing tends to be higher, making it less suitable for mass production.
Variety of Materials Available
Injection Molding: A Wide Array of Choices
Rating: ★★★★★
Injection molding boasts a broad spectrum of materials, making it highly versatile in terms of material selection. These include:
- Common Plastics: Such as ABS, Polycarbonate (PC), Polystyrene (PS), Polypropylene (PP), Polyethylene (PE), etc.
- Engineering Plastics: Like Nylon (PA), Polybutylene Terephthalate (PBT), Polyether Ether Ketone (PEEK), etc.
- Special Plastics: Including Thermoplastic Elastomers (TPE), Thermoplastic Rubber (TPR), etc.
- Modified Materials: Physical and chemical modifications of basic resin materials enhance certain properties, leading to thousands of derivative plastic types. Hence, injection molding materials are far more diverse compared to those used in 3D printing.
3D Printing Materials: Growing but Limited
Rating: ★★★☆☆
The range of materials for 3D printing is expanding, but it’s still less diverse than injection molding. Available materials include:
- Thermoplastics: Like PLA, ABS, PETG, TPU, Nylon (PA), etc.
- Photopolymer Resins: Suitable for SLA, DLP technologies, with a variety of types.
- Metal Materials: Such as Titanium alloys, Stainless steel, Aluminum alloys, Cobalt-chromium alloys, etc.
- Composite Materials: Including carbon fiber and glass fiber reinforced plastics.
- Special Function Materials: Like transparent PMMA, conductive materials, biocompatible materials, etc.
- Ceramic Materials: Used for high-temperature and high-hardness applications.
It’s reported that there are over 200 types of 3D printing materials to date, which is significantly fewer than those available for injection molding. Moreover, many materials and their processing equipment are not yet widely available. The most common and readily accessible materials are: Photopolymer Resins, Nylon (with and without glass fiber), PMMA (transparent), and TPU (elastic material).
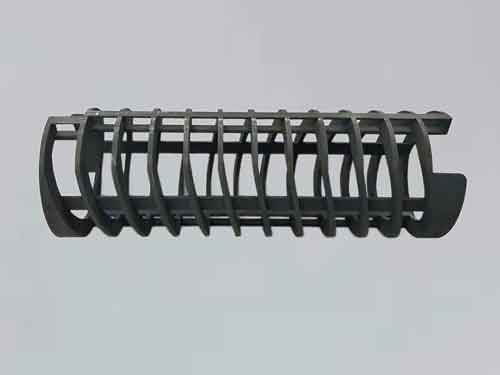
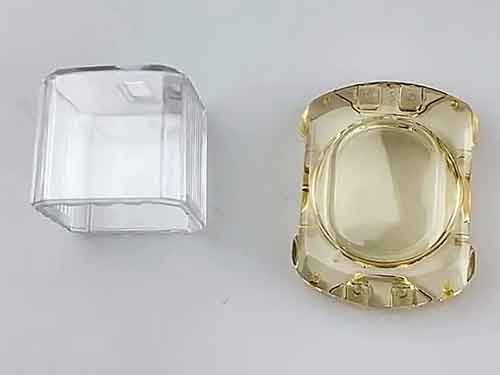
injection molding vs 3d printing strength comparison
In this section, we focus on comparing plastic materials used in 3D printing with those used in injection molding. We will not consider metal printing materials due to their higher mechanical performance, longer lifespan, and relatively high cost, making them less common in general applications.
Strength
- Injection Molding Materials: Rating: ★★★★☆
- Generally, these materials exhibit higher strength as they are formed under high pressure, leading to a denser molecular structure. Engineering plastics, such as reinforced Nylon and PPS, can have strength comparable to aluminum alloys.
- 3D Printing Materials: Rating: ★★☆☆☆
- The strength of 3D printed materials can be lower, primarily because most 3D printing techniques build objects layer by layer, resulting in weaker interlayer bonding. Although SLS-printed Nylon is relatively strong, it’s still noticeably weaker than injection-molded reinforced Nylon.
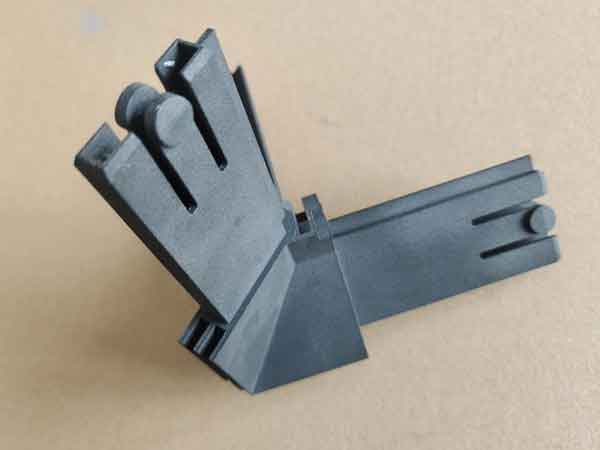
Durability and Lifespan
- Injection Molding Materials: Rating: ★★★★☆
- These materials usually offer high durability and are suitable for long-term and repeated use applications.
- 3D Printing Materials: Rating: ★★☆☆☆
- The durability and lifespan of 3D printed materials may be lower, especially under mechanical stress and environmental influences. For instance, photopolymer resins can undergo permanent deformation under moderate pressure over time and may discolor after several months.
Heat Resistance
- Injection Molding Materials: Rating: ★★★★☆
- High-performance plastics such as PEEK or PSU can be selected for excellent heat resistance.
- 3D Printing Materials: Rating: ★★☆☆☆
- The heat resistance is generally lower, especially for commonly used materials like photopolymer resins, PLA, and ABS. However, specialized high-temperature resins and metal materials are available.
For example, a Nylon sample created through 3D printing developed noticeable bubbles when painted and heated to 80-90 degrees Celsius.
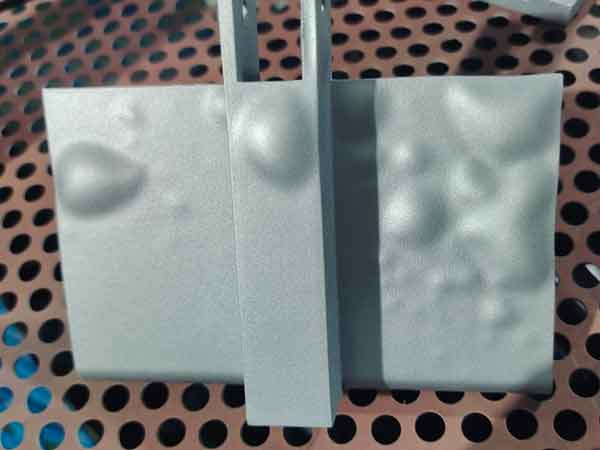
Surface Quality
The surface quality of products manufactured through injection molding and 3D printing varies significantly due to their distinct manufacturing processes and material characteristics. Here’s a comparison of the two methods in terms of surface quality:
Surface Quality of Injection Molded Products: Exceptional
Rating: ★★★★★
- Smoothness: Injection molded parts usually have a very smooth surface, as they are formed under high pressure in precision-made molds.
- Detail Replication: Capable of precisely replicating the mold’s details, including fine textures and patterns.
- Consistency: Products from each production cycle have highly consistent surface quality.
- Post-Processing: Typically requires little or no post-processing, other than removing minor edge burrs.
Surface Quality of 3D Printed Products: Good with Limitations
Rating: ★★★☆☆
- Layered Structure: Due to the layer-by-layer construction in 3D printing, surfaces may show a layered texture, especially more noticeable at higher layer heights.
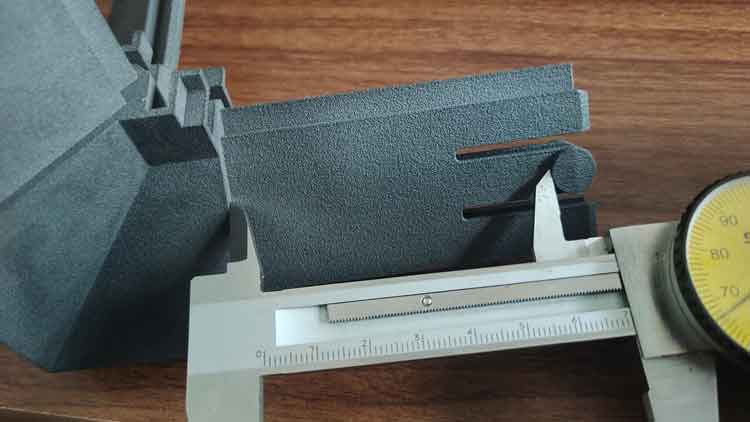
- Detail Limitations: While capable of printing complex structures, achieving extremely fine details and very smooth surfaces can be challenging.
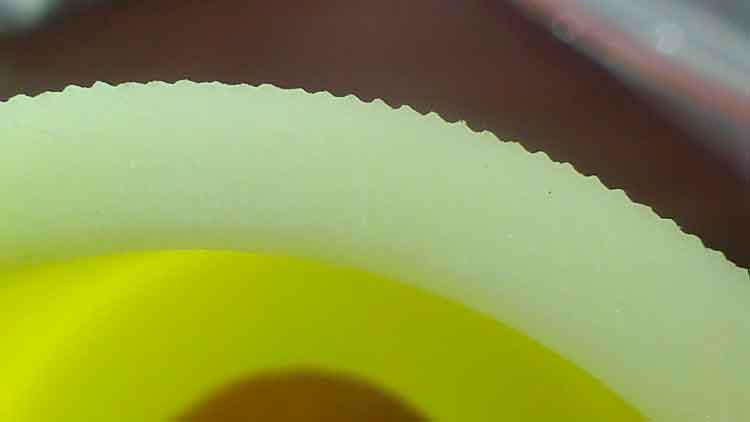
- Consistency: Surface quality may vary depending on printing settings, orientation, and materials used.
- Post-Processing: Often requires more post-processing, such as sanding, polishing, or chemical smoothing, to enhance surface smoothness.
Conclusion
Injection molded products generally surpass 3D printed products in surface quality, particularly in terms of smoothness and detail accuracy. However, advancements in 3D printing technology, especially in stereolithography (SLA) and selective laser sintering (SLS), have significantly improved surface quality, making it increasingly comparable to traditional injection molding standards.
Design Flexibility
3D Printing: Highly Versatile
Rating: ★★★★★
- Complex Designs: 3D printing excels in allowing complex designs and geometrical structures, such as hollow structures, intricate internal channels, and fine details. It enables the creation of designs that are not feasible with traditional manufacturing methods.
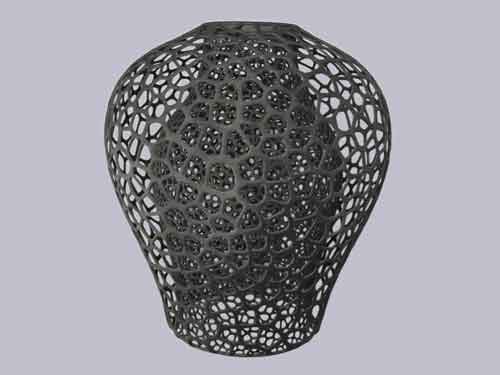
Injection Molding: Constrained by Technical Limitations
Rating: ★★★☆☆
- Design Considerations: The design process must consider how the mold will open and close, how cores will be removed, and how the product will be ejected from the mold. Factors like wall thickness and draft angles also play a crucial role.
Ease of Design Modification
3D Printing: Seamless Adjustments
Rating: ★★★★★
- Model Adjustments: Modifying a design in 3D printing is as simple as adjusting the digital model, with no additional costs or significant time investment. This allows for rapid iteration at a lower cost.
Injection Molding: Challenging and Costly Modifications
Rating: ★☆☆☆☆
- Mold Adjustments: Making design changes in injection molding can be a cumbersome process. In many cases, it requires the creation of a new mold, which is both time-consuming and expensive.
Comparative Table of 3D Printing vs. Injection Molding
Criteria | 3D Printing | Injection Molding |
---|---|---|
Production Timeline | ★★★★★ | ★★☆☆☆ |
Initial Investment Costs | ★★★★☆ | ★★☆☆☆ |
Mass Production Efficiency | ★★☆☆☆ | ★★★★★ |
Material Variety | ★★★☆☆ | ★★★★★ |
Material Strength and Durability | ★★☆☆☆ | ★★★★☆ |
Surface Quality | ★★★☆☆ | ★★★★★ |
Design Flexibility | ★★★★★ | ★★★☆☆ |
Ease of Design Modification | ★★★★★ | ★☆☆☆☆ |
This table serves as a quick reference for comparing key aspects of 3D printing and injection molding, providing a clearer understanding of where each method excels and where it may fall short.
Summary
In summary, 3D printing excels in design flexibility, rapid prototyping, and low initial costs, making it ideal for small-scale and custom projects. Injection molding, however, is superior in material strength, surface quality, and cost-effectiveness for large-scale production. The choice between these two methods depends on project specifics like volume, budget, and desired quality, with each method offering distinct advantages tailored to different manufacturing needs.