Understanding the Fundamentals of Polycarbonate in Injection Molding
Polycarbonate (PC) is an amorphous thermoplastic material, a high polymer containing carbonate groups (-O-C(=O)-O-) in its molecular chain. It is synthesized through a polymerization reaction involving Bisphenol A (BPA) and Phosgene (COCl2). Known as a high-performance thermoplastic, PC is widely used for its outstanding transparency, heat resistance, and impact resistance.
Basic Parameters of PC
- Density: Typically ranges from 1.20 to 1.22 g/cm³.
- Melting Point: Approximately 260°C to 270°C.
- Injection Molding Temperature: 270-320°C.
- Glass Transition Temperature (Tg): About 135-150°C.
- Cantilever Beam Notch Impact Strength: Around 60 KJ/m2.
- Tensile Strength: Approximately 60 to 70 MPa (Megapascals).
- Flexural Strength: Can reach about 90 to 120 MPa.
- Transparency: Up to 90% in the visible light range.
- Chemical Resistance: Good resistance to weak acids and bases, but sensitive to certain solvents and strong chemicals.
- Water Absorption: Good, with a low absorption rate of about 0.3%. Tends to hydrolyze at high temperatures.
Advantages of Polycarbonate (PC)
- High Transparency and Gloss: PC material boasts excellent optical properties with a light transmission rate of 90%, comparable to glass but lighter and less prone to breakage. Along with PMMA and PS, it forms the most commonly used transparent plastics.
- Exceptional Heat and Cold Resistance: PC remains stable at higher temperatures (usually between 140°C and 150°C) and can be used in temperatures as low as -60°C to -40°C without becoming brittle.
- High Impact Resistance: The impact resistance of PC is 250-300 times that of ordinary glass and 30 times that of acrylic sheets of the same thickness, making it a highly durable material.
- Flame Retardant: PC naturally possesses flame-retardant properties, achieving a UL94 V2 rating even without additives.
- Excellent Electrical Insulation: This makes it widely applicable in the electronics and electrical fields.
- Good Creep Resistance and Dimensional Stability during Processing.
Disadvantages of Polycarbonate:
- Susceptibility to Scratching: PC material is relatively soft and prone to scratching. This can be an issue in applications requiring transparency and abrasion resistance. Therefore, it’s common to apply a scratch-resistant coating to the surface.
- Prone to Stress Cracking: PC material can develop stress cracks when subjected to mechanical stress or certain chemicals, especially at edges or weak points. This is caused by internal stresses, possibly due to improper processing or excessive force during assembly. Stress cracking not only affects the appearance but also significantly reduces mechanical strength. To mitigate this risk, stress management during design and processing, as well as avoiding contact with certain chemicals, is important.
- Processing Difficulties: The processing difficulty of PC is also reflected in its relatively low fluidity and high melting point, usually between 220°C and 260°C. This requires higher heating temperatures in injection molding or other thermoplastic processing, increasing energy consumption and demanding more from processing equipment. Additionally, the lower fluidity of PC compared to some other plastics can lead to insufficient or uneven filling in complex or slender mold designs.
- UV Sensitivity: PC can yellow and become brittle when exposed to UV light for extended periods. To prevent this, UV stabilizers are often added or a protective coating is applied to the surface.
- Chemical Sensitivity: PC is sensitive to certain chemicals, particularly some solvents, cleaners, and greases like alcohol, ketones, acids, and bases, which can cause cracking or degradation.
- High Cost: Compared to other types of plastics, PC generally comes at a higher cost.
- Environmental and Health Concerns: One of the main components of PC is Bisphenol A (BPA), an endocrine disruptor that has attracted attention. The potential health impacts of BPA, especially in infant and children’s products, have become a focus of public and regulatory concern.
Applications of Polycarbonate in Injection Molding
Polycarbonate (PC) plays a crucial role in various injection molding products due to its unique characteristics and is widely used in the following areas:
Transparent Casings and Goggles: PC’s high transparency and strength make it ideal for manufacturing various transparent casings and goggles.
- Optical Lenses: PC is extensively used in the optical field. For instance, it is used to produce LED lamp lenses, automotive light lenses, and car headlight covers. These applications take full advantage of PC’s light transmission and heat resistance.
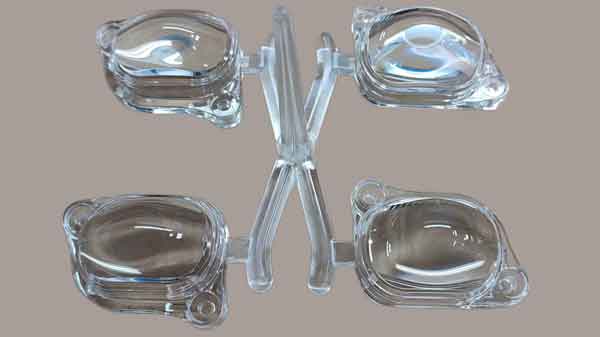
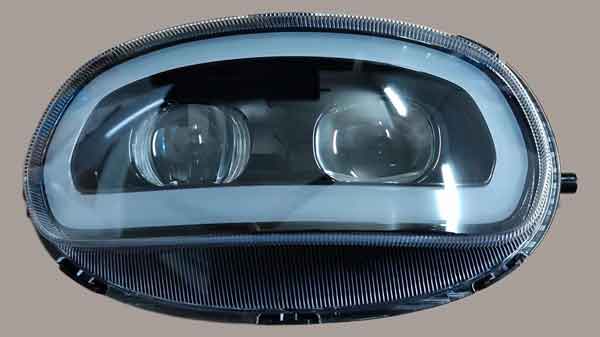
Casings for Electrical Products: PC is also widely used in manufacturing casings for electrical products, such as electric meter housings. The choice of PC is mainly due to its flame-retardant properties, weather resistance, and high strength and toughness, ensuring the safety and durability of electrical products.
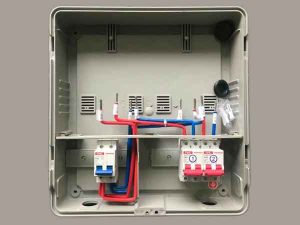
Optical Discs: Optical discs, such as CDs and DVDs, are typically made of PC material, benefiting from its excellent optical properties and processability.
Safety Helmets: The high impact resistance of PC makes it an ideal material for manufacturing safety helmets, which are extensively used in construction, sports, and other fields requiring head protection.
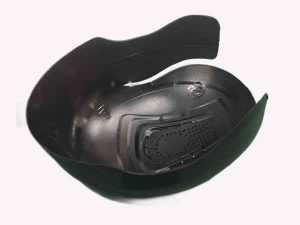
Electronic Device Casings: Including casings for computers and headphones, the application of PC material provides a solution that is lightweight, durable, and aesthetically pleasing.
These applications demonstrate the widespread use of PC in modern industry and everyday life. Its features, such as high transparency, strength, and flame retardancy, play an important role in many fields.
Types of PC and Modified PC
Let’s quickly understand the various types of Polycarbonate (PC) and the nature of modified PC. Modified PC refers to the materials obtained by adding different reinforcing materials or additives to the base PC resin to improve or enhance its original properties. Common types of modified PC include:
High and Low Molecular Weight PC: High molecular weight PC has longer chain lengths, typically showing higher strength, better heat resistance, and superior mechanical properties. It’s suitable for high-performance applications like bulletproof materials and high-end mechanical parts. Conversely, low molecular weight PC, with shorter chain lengths, is easier to process and mold but usually means lower mechanical strength and heat resistance. This type of PC is more suitable for general consumer products and non-heavy-duty applications.
Glass Fiber Reinforced PC: Reinforcing PC with glass fibers enhances its mechanical strength and dimensional stability, making it more suitable for applications requiring high strength and rigidity.
Flame Retardant PC: The addition of flame retardants improves PC’s flame retardant properties. Unmodified, PC has a V2 flame retardant rating, insufficient for many products. With added flame retardants, it can reach a V0 rating. Flame retardants can be halogenated or non-halogenated.
UV Resistant PC: By adding UV stabilizers, the weather resistance of PC for outdoor use is enhanced, reducing discoloration and performance degradation due to prolonged UV exposure.
PC/ABS Alloy: Mixing PC with ABS (Acrylonitrile Butadiene Styrene) combines the high strength and heat resistance of PC with the ease of processing and surface smoothness of ABS, along with stress crack resistance. This is widely used in automotive parts, electronic device casings, and more.
Carbon Fiber Reinforced PC: Incorporating carbon fibers improves the material’s strength and thermal stability, suitable for lightweight and high-performance applications in aerospace and automotive industries.
PC/PBT or PC/PET Alloy: By blending with PBT (Polybutylene Terephthalate) or PET (Polyethylene Terephthalate), chemical resistance and impact resistance are enhanced, often used for products requiring chemical corrosion resistance and high impact strength.
Transparent PC: Although PC is inherently transparent, specific modifications can further enhance its transparency and optical properties, suitable for optical products and decorative items that require high transparency.
PC/ASA Alloy: Alloying with ASA (Acrylate-Styrene-Acrylonitrile) improves weatherability and UV resistance, suitable for applications that are exposed outdoors for long periods.
These modified PC materials, with their unique combination of properties, find widespread applications in various industrial fields. Through modification, the application range of PC has been greatly expanded, meeting more stringent or specific performance requirements.
Injection Molding Parameters for Polycarbonate (PC)
Understanding the right parameters for injection molding of PC is crucial for optimal product quality. Here’s an overview:
Runner and Gate Design
- Runners: Design runners to be as thick and short as possible, with minimal bends. Round cross-sections and polished runners help reduce melt flow resistance.
- Gates: Any form of gate can be used, but the diameter should not be less than 1.5mm. For transparent parts, large gates are generally used to avoid defects like bubbles and stress marks.
Drying Temperature and Time
- PC materials require thorough drying before processing, typically at 100°C to 120°C for 3 to 4 hours to avoid surface defects and product cracking.
Key Injection Molding Parameters
- Injection Temperature: Usually between 270°C and 320°C, this range is crucial for melting the PC material for injection.
- Mold Temperature: Set around 80°C to 120°C. Higher temperatures may be needed for complex shapes or thin walls but should not exceed the thermal deformation temperature of the mold. Proper mold temperature helps reduce molding stress and improve product transparency.
- Injection Pressure: Generally between 50 to 150 MPa. Higher pressure helps the PC material to fill the mold completely.
- Holding Pressure: The size and duration of holding pressure significantly impact the internal stress of PC products. Too little pressure can lead to vacuum bubbles or surface sinking, while too much pressure can cause high internal stress near the gate. A common approach is high material temperature with low holding pressure.
- Injection Speed: Adjust according to the specific shape and size of the product. Thin-walled or long-flow products may require faster injection speeds. Otherwise, medium or slow speeds are preferable, ideally with multi-stage injection, typically slow-fast-slow.
- Screw Speed: Due to PC’s high viscosity, the screw speed shouldn’t be too high to facilitate plasticization, venting, and maintenance of the injection machine. Typically, it should be controlled between 30-60 rpm, with back pressure at 10-15% of the injection pressure. Proper screw speed ensures uniform heating and mixing.
- Machine Size: The optimal product weight is about 40 to 60% of the injection machine’s capacity. If the machine’s capacity is measured in polystyrene ounces, reduce by 10%.
- Screw: Given PC’s good thermal stability and high viscosity, a screw with a length-to-diameter ratio (L/D) of more than 20:1, at least 15:1, is ideal, implying a longer and thinner screw. The compression ratio should be 1.5:1 to 3:1. The sliding ring type should be used for the check valve at the screw’s front end, with a resin flow gap of at least 3.2mm.
- Clamping Pressure: Calculate based on the product’s projected area, with 0.47 to 0.78 tons per square centimeter (or 3 to 5 tons per square inch).
- Back Pressure: Lower back pressure helps reduce material degradation, typically between 5 to 20 MPa.
- Cooling Time: Adjust based on product thickness and mold temperature to ensure full cooling and setting.
These parameters should be adjusted and optimized according to actual machine conditions, material characteristics, and product design requirements. Correct injection molding parameters are essential for ensuring product quality and production efficiency.
Conclusion
In conclusion, mastering polycarbonate in injection molding opens up a realm of high-performance applications due to its unique properties. By understanding the right techniques, parameters, and modifications, manufacturers and designers can harness the full potential of PC, ensuring durable, high-quality, and versatile products in a wide range of industries.
Comments are closed.