Why Plastic Annealing is Required for Some Injection Molded Parts
The purpose of annealing plastic is to address some of the issues that arise during the injection molding of plastic products. In the process of plastic injection molding, internal stresses often develop within the product due to factors like temperature and pressure. If these internal stresses become too great, they can lead to quality issues such as unstable dimensions, warping, deformation, or even cracking in the final product. Just as steel requires annealing, plastic products can also be improved through the annealing process.
Annealing primarily involves heating the plastic product to a specific temperature and then allowing it to cool slowly under controlled conditions. This process enables the molecules within the plastic to realign, thereby reducing or eliminating internal stresses and enhancing the dimensional stability and overall quality of the product.
In addition to annealing, post-processing of plastic products includes moisture conditioning. Moisture conditioning involves increasing the humidity of the plastic material, which can enhance the toughness of the material, especially important for PA (polyamide) materials. By adjusting the material’s moisture content, its mechanical properties can be improved, making the final product more durable and stable in use.
In summary, annealing and moisture conditioning are critical steps in plastic processing. They help to improve the performance and quality of the products, ensuring the stability and durability of plastic products in everyday use.
Causes of Internal Stress in Injection Molded Products
Internal stress in injection molded products can arise from several factors:
- Uneven cooling of plastic parts within the mold.
- Uneven plasticization.
- Inconsistent crystallization and orientation of the plastic molecules within the plastic part.
- The use of metal inserts, which create a significant difference in temperature and cooling speed near the insert compared to adjacent areas.
These factors lead to inconsistent shrinkage in different parts of the plastic piece, inevitably resulting in internal stress. The presence of internal stress often causes deformation or cracking in the plastic pieces during their use. Therefore, it’s crucial to find ways to eliminate these stresses.
Depending on the characteristics of the plastic and the requirements for its use, the pieces can undergo annealing and moisture conditioning treatments. These processes are tailored to reduce internal stresses and enhance the overall quality and durability of the plastic products.
Note: From the image, it can be observed that the stress area below the V-notch has disappeared after the heat treatment.
Steps of Plastic Annealing
Plastic annealing is a thermal process designed to reduce internal stresses in plastic parts, which may arise from uneven cooling or during the manufacturing process. The annealing process typically involves the following steps:
Heating: The method involves placing the plastic parts in an oven or a liquid medium (such as hot water, hot mineral oil, glycerin, ethylene glycol, or liquid paraffin) at a specific temperature for a certain period, followed by slow cooling. The annealing temperature is generally controlled to be 10-20°C higher than the part’s service temperature or 10-20°C lower than the plastic’s heat distortion temperature. The temperature should not be too high to avoid warping and deformation of the part, nor too low, as it would not achieve the intended post-treatment effect. The duration of annealing depends on the type of plastic, temperature of the heating medium, shape and wall thickness of the part, and precision requirements of the part.
Maintaining Temperature: The parts are maintained at this temperature for a certain period to allow the internal stresses to redistribute. The duration depends on the type of plastic and the thickness of the part.
Slow Cooling: After completing the annealing process, it is essential to cool down the parts slowly to prevent the formation of new stresses. This is usually achieved by allowing the parts to cool naturally inside the oven, gradually reaching room temperature after the heating source is turned off.
Each type of plastic material has its specific annealing temperature and duration. For example, materials like ABS, polycarbonate, and nylon each have different annealing requirements. Therefore, the annealing process must be adjusted according to the specific type of plastic used. Proper annealing treatment can significantly improve the dimensional stability of plastic products and reduce the likelihood of cracking.
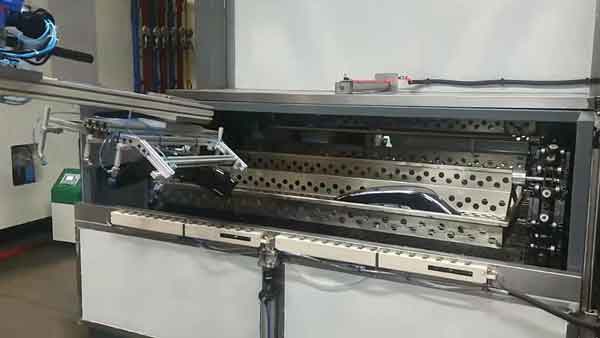
Note: Displayed here is the heat treatment process for the headlight cover of a car. The product material is PC (Polycarbonate), and the treatment is conducted at a temperature of 130°C for a duration of 3 hours.
Results of Annealing Treatment
The annealing process yields significant results in the treatment of plastic parts. Firstly, it eliminates internal stresses and stabilizes dimensions. This aspect is crucial for maintaining the shape and size consistency of plastic products.
For crystalline plastics, annealing can also enhance the degree of crystallinity and stabilize the crystalline structure. This improvement typically increases the elastic modulus and hardness of the material. However, it’s important to note that this process may reduce the fracture elongation rate.
It’s worth mentioning that not all plastic parts necessarily require post-treatment. For instance, polyoxymethylene (POM) and chlorinated polyether plastics, despite having internal stresses, can gradually eliminate these stresses on their own. This is due to the high flexibility of the polymers and their lower glass transition temperature. Therefore, in cases where the requirements for plastic parts are not stringent, post-treatment might be unnecessary. This flexibility in the post-treatment process allows for a more tailored approach depending on the specific needs and characteristics of the plastic material in question.
Annealing Processes for Common Plastics
The following information provides recommended annealing temperatures and mediums for several common types of plastics. This quick reference guide helps to understand the annealing processes specific to different plastic materials.
Plastic Type | Medium | Annealing Temperature (°C) |
---|---|---|
ABS | Water or Air | 60~75 |
PS | Water or Air | 60~70 |
PMMA | Air | 75 |
POM | Oil or Air | 160 |
PP | Air | 150 |
HDPE | Water | 100 |
PC | Oil or Air | 120~130 |
PET | Nitrogen-Filled Furnace | 130~150 |
PBT | Chlorine-Filled Furnace | 130~150 |
PA6 | Water or Oil | 100-130 |
PA66 | Water/Potassium Acetate (1/1.25) 3~6 | 100 |
This table serves as a general guide. It’s important to note that the exact annealing temperature and medium may vary depending on the specific grade of plastic and the desired properties of the final product. Adjustments might be necessary based on the thickness, size, and complexity of the plastic part.
Conclusion
In summary, heat treatment is not a commonly used process for injection molded products. Most of the time, products are allowed to age naturally over time to release stress. Additionally, besides annealing, there are now methods to release internal stresses through ultrasonic treatment and the application of high pressure. However, understanding the process of plastic annealing provides a more comprehensive insight into the production of injection molded parts, enabling its use in necessary situations.