Understanding the Plastic Toy Injection Molding
Plastic toys have carved a significant niche in the toy industry due to their diversity, durability, and cost-effectiveness. Their range is extensive, encompassing building blocks, model cars and airplanes, and even remote-controlled toys. Moreover, plastic is also a primary material in children’s ride-on toys and various outdoor playthings like slides and water guns. Some electronic toys are also predominantly made of plastic.
Compared to traditional materials like metal, wood, and fabric, plastic is more frequently used in toys. This article aims to provide a comprehensive understanding of plastic toys, from their advantages and disadvantages to their production and design methods, and even the post-production processes. We hope this information will help you make more informed choices and better understand plastic toys.
Advantages of Plastic Injection Molded Toys
Plastic injection molding for toy production is an efficient and precise manufacturing method. In this process, melted plastic is injected into a mold and cools to form an exact replica of the mold cavity. The advantages of this technology include:
High-Efficiency Production: Injection molding allows for the rapid mass production of toys. When combined with automated inspection and packaging, it significantly enhances production efficiency, especially for large-scale runs.
Precision in Detail: Utilizing precise molds, injection molding can create toys with complex shapes and rich details. This precision is particularly crucial for toys requiring intricate designs, such as action figures and detailed model vehicles.
Cost-Effectiveness: Although the initial investment, like mold manufacturing costs, can be high, the efficiency of mass production means that the cost per toy is relatively low in the long term.
Material Diversity: Injection molding technology can use various types of plastics, including more environmentally friendly options. This allows manufacturers to choose different materials based on the specific needs of the toy and market trends.
Diverse Colors and Appearances: During the production process, different colors and decorative features can be easily added. Plastic can be produced in a wide range of colors, and additional processes like painting or electroplating further enrich and enhance the toy’s appearance.
In summary, plastic injection molding offers an efficient, economical, precise, and versatile method of toy production. These advantages make injection molding technology a crucial player in the toy industry.
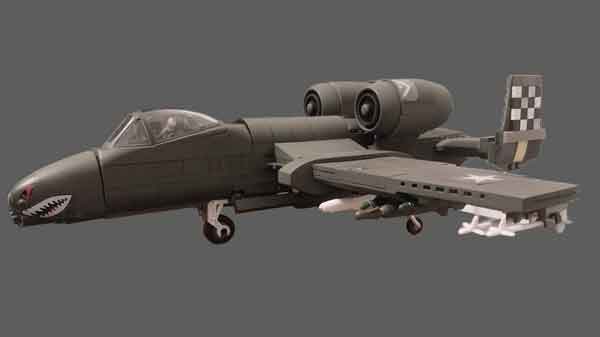
Disadvantages of Injection Molded Toys
Despite the many advantages of producing toys through injection molding, there are some significant drawbacks that cannot be overlooked:
Limitations in Use Conditions: Plastic toys may melt under high temperatures. Also, the strength of plastic generally falls short of materials like metal, which could impact the toy’s durability and lifespan.
High Initial Costs: Creating injection molds involves substantial design and manufacturing costs. This investment may not be economical for small-scale production, making it more suitable for mass production.
Environmental Concerns: The production and disposal of plastics can have adverse environmental impacts, especially in the case of non-biodegradable plastics. A large number of discarded plastic toys can lead to severe environmental pollution.
Health Risks: Certain types of plastics, along with surface paints or electroplating coatings, might release harmful substances during production and usage. Strict quality control is required during the manufacturing process to ensure the safety of the toys.
In conclusion, while injection molded toys have distinct manufacturing advantages, they also face limitations and challenges regarding use conditions, costs, design, environmental impact, and health concerns. These factors need to be thoroughly considered and addressed during the production and usage stages.
Toy Injection Molding Design Process and Software Use
The design process for toy injection molding typically involves two main aspects: aesthetic design and functional design. Different designers may focus on different stages, so collaboration among multiple professionals is often required.
1. Aesthetic Design
- Traditional Methods: Traditionally, product designers created toy prototypes using drawing and sculpting, and then converted these sculptures into 3D files using 3D scanning technology.
- Modern Software Tools: Increasingly, designers are using 3D software for design purposes. These software packages, including Rhino, Maya, 3DS Max, Cinema 4D, and Zbrush, are more suitable for complex aesthetic designs, offering richer details and greater creative freedom.
2. STL Files
- Characteristics of STL Files: These design software tools typically generate STL files, which contain information about the object’s surface geometry in the form of triangular facets. Although common in 3D printing, the STL format mainly represents surfaces and lacks information about internal structures or cutting paths.
3. 3D Modeling and CNC Processing
- Limitations of STL Files: STL files do not contain details necessary for CNC processing, such as precise cutting paths and material information, rendering them unsuitable for direct use in CNC machining.
- File Conversion: For mold processing, STL files usually need to be converted into formats like STEP or IGES. This requires designers to not only be proficient in 3D modeling software but also have specialized knowledge in mold design.
- Conversion Process: For simpler shapes, software like UG can be used directly for conversion. However, for more complex designs with numerous details, pre-processing with software like Geomagic may be necessary before conversion with UG. This process can be very time-consuming, sometimes even exceeding the workload of the original aesthetic design.
In summary, toy injection molding design is a process that involves a wide range of skills and software applications. From the initial aesthetic design to the final mold manufacturing, each step requires precise handling and professional technical support. Designers need to find a balance between creativity and technical process to ensure that the design is both aesthetically pleasing and practical.
Key Considerations in Manufacturing Toy Injection Molds
When manufacturing toy injection molds, several critical aspects must be taken into account:
Precision in Appearance: The design and appearance of plastic toys are crucial. Molds must replicate every detail of the design accurately to ensure that the final product faithfully conveys the original design’s style. Even slight deviations in dimensions can alter the overall appearance, making precision in critical areas of the mold essential.
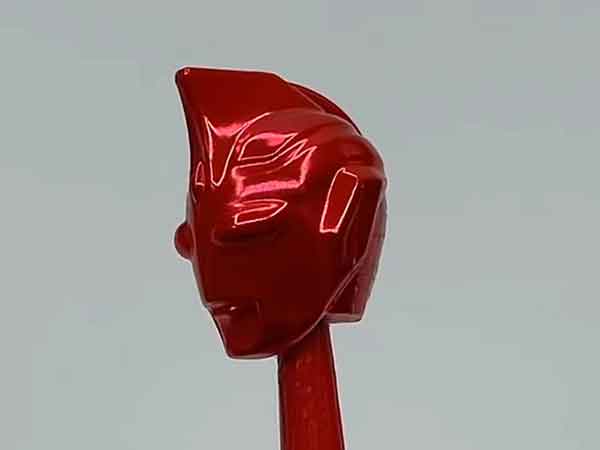
Balancing Precision and Cost: While ensuring dimensional accuracy and crucial details, cost control is also a vital factor. Optimization in the choice of processing equipment and techniques is necessary to achieve the best balance between cost and precision.
Cooling System Design: Given the mass production nature of plastic toys, the design of the mold’s cooling system is especially important. Uneven cooling can lead to warping or shrinkage of the product, so a well-designed cooling system is crucial for maintaining product quality and improving production efficiency.
Use of Family Molds: To reduce costs, the use of composite molds has become increasingly common. For instance, a toy pen composed of multiple parts can be produced using a single composite mold, with robotic arms used for automated production, significantly reducing production costs.
Choice of Mold Steel: Common toy parts do not require high-temperature materials or fiberglass-reinforced materials, so the requirements for mold materials are relatively lower. Materials like P20, 718H, and NAK80 are often used for standard toy molds. However, for toys with higher aesthetic demands, higher-grade mold materials such as S136(H), 2083, 420, PAK90, etc., are needed to ensure a high-quality appearance of the products.
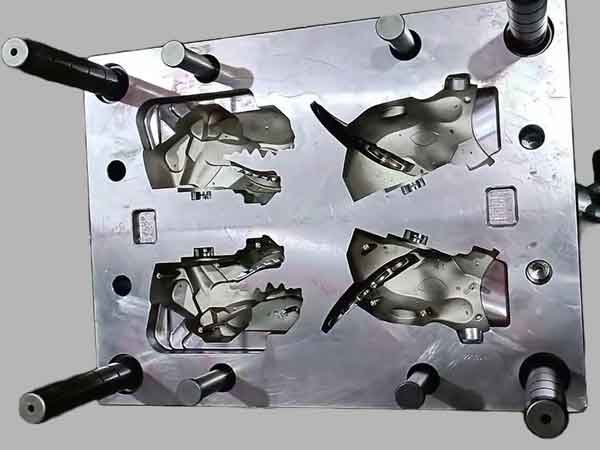
In summary, the design and manufacturing of toy injection molds involve a comprehensive consideration of appearance precision, cost-effectiveness, production efficiency, and material selection. Properly addressing these issues is key to ensuring toy quality and reducing production costs.
Common Plastics Used in Toy Manufacturing
A variety of plastics, each with its unique properties, are commonly used in toy manufacturing, suitable for different types of toys. Here are some of the frequently used plastics and their applications in toy production:
Polyethylene (PE):
- Characteristics: Good flexibility, impact resistance, safe and non-toxic.
- Applications: Often used in manufacturing infant and toddler toys, beach toys, slides, and swing toys.
Polypropylene (PP):
- Characteristics: Higher hardness, good heat resistance, and less prone to breaking.
- Applications: Suitable for making children’s tableware, safety seats, and some durable toys.
Polyvinyl Chloride (PVC):
- Characteristics: Strong plasticity, easy to color, and resistant to chemical corrosion.
- Applications: Used in the production of inflatable toys, dolls, action figures, swimming rings, etc.
Polystyrene (PS):
- Characteristics: High transparency and easy to process.
- Applications: Commonly used for model kits, transparent toy components, and educational toys.
ABS Resin:
- Characteristics: High strength, smooth surface, easy to color, and moderate heat resistance.
- Applications: Widely used in high-quality building blocks, electronic toys, and model toys.
Polycarbonate (PC):
- Characteristics: Good transparency, high strength, and impact resistance.
- Applications: Used in making protective face shields, transparent windows for toy vehicles, etc.
Each of these plastics brings different benefits to toy manufacturing, allowing for a wide range of products that cater to various needs and preferences.
Surface Printing on Plastic Toys
The surface printing and decoration of plastic toys involve a variety of techniques, each with its unique advantages and suitable applications. Here are some common surface treatment techniques for plastic toys, including the in-mold decoration technology:
Spray Painting: This method involves coloring the toy’s surface by spraying paint, suitable for various types of plastics, providing a smooth and uniform color effect. However, only one color can be sprayed at a time.
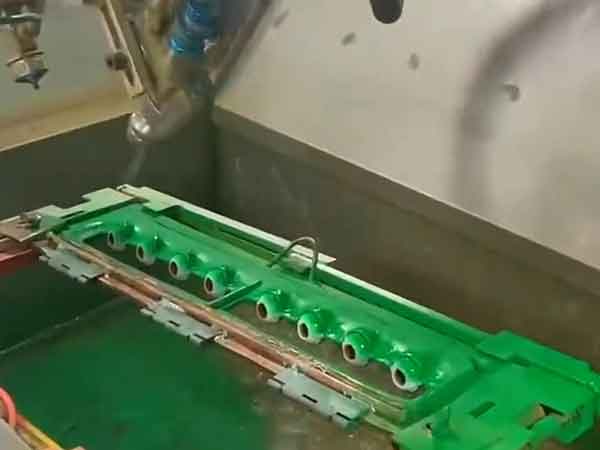
Pad Printing: This technique uses a special silicone pad to transfer patterns from the printing plate to the toy’s surface. It’s ideal for complex or irregular surfaces and can precisely replicate intricate patterns, but the printing area and thickness are limited, and the color brightness might not be optimal. Only one color can be printed at a time.
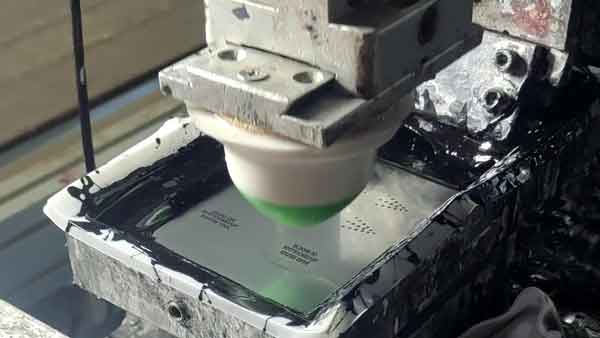
Heat Transfer Printing: In this method, patterns are transferred from transfer paper to the toy’s surface using heat. It creates lasting and vivid patterns, suitable for large, smooth surfaces. Since the pattern is printed on the transfer paper, a wide range of colors is available.
Water Transfer Printing: This technique involves printing patterns on a water-soluble film, which is then placed on water. The pattern is transferred to the item’s surface using water pressure. It’s particularly suitable for complex shapes, offering comprehensive coverage. Like heat transfer printing, there are no limits on color varieties.
In-Mold Decoration (IMD): This advanced decoration technique involves placing a patterned film inside the injection mold. As the plastic is molded, the pattern on the film integrates firmly onto the product’s surface. This method not only provides a rich visual effect but also enhances the product’s wear and scratch resistance. However, it is generally used on regular surfaces like planes, cylinders, or cones.
Each technique has its characteristics, and the choice of which to use depends on the toy’s material, design requirements, and production costs. In-mold decoration technology, due to its durability and high-quality effect, is increasingly used in the manufacturing of high-end toy products.
Conclusion
In conclusion, this article delves into the intricate world of plastic toy manufacturing, highlighting the nuances of injection molding, design intricacies, mold making, and diverse surface printing techniques.
It showcases how each step, from conceptualization to final production, blends creativity with technical precision. This industry’s commitment to quality and innovation not only meets diverse consumer needs but also continuously evolves, shaping the future of toy manufacturing in a dynamic and vibrant market.