What is 2 Shot Injection Molding
Two-shot injection molding, also known as dual-shot or double injection molding, is an efficient injection molding technology that creates composite components made of two different colors or types of plastic materials within a single molding cycle.
This process requires a specialized two-shot injection molding machine equipped with two separate sets of screws and barrels. This technology is capable of producing components with both aesthetic appeal and functional strength, finding widespread applications in the automotive, consumer electronics, and medical equipment industries.
The Process of 2 Shot Injection Molding
The process of two-shot molding is outlined as follows, highlighting the intricate steps involved in creating a composite component within a single molding cycle:
Mold Design and Manufacture
Two-shot molding necessitates the use of a specialized two-shot injection molding machine and precisely designed molds. The design of the mold must take into account the flow, cooling, and solidification characteristics of both materials to ensure they combine correctly within the mold. The steps are as follows:
First Injection: The process begins with the injection of the first material into one of the injection units of the molding machine, forming part of the product. Once this step is completed, the partially formed component remains fixed within the mold or is moved to another position through rotation or shifting of the mold.
Mold Rotation or Shifting: For some two-shot molding processes, the semi-finished product from the first injection needs to be transferred within the mold to a second injection position. This can be achieved by rotating or shifting the mold, depending on the design of the two-shot molding machine used.
Second Injection: After the first part has solidified and been moved to the second position, the second material is injected into the mold through another injection unit, bonding with the first part to form the final product. This step requires precise control to ensure good adhesion between the two materials.
Cooling and Solidification: Following the injection of the second material, the entire component cools and solidifies within the mold. This stage is critical for the quality of the product, necessitating precise control over cooling speed and time.
Mold Opening and Ejection: After cooling and solidification, the mold is opened, and the finished two-color product is ejected.
This detailed process showcases the technical complexity and precision required in two-shot molding, allowing for the production of high-quality, multifunctional components used across various industries.
This video shows the trial process of 2-shot molding. Because the product is small and has an undercut feature, it can’t be automatically removed from the mold. It might get stuck on the mold’s lifter, so it needs to be taken out manually.
Advantages and Disadvantages of Two-Shot Molding
Two-shot molding has the distinct advantage of producing complex, high-quality products with diverse appearances in a single molding cycle. It can reduce post-processing steps, enhance production efficiency, and lower costs. However, this technology demands high requirements for mold design and manufacturing, leading to relatively high initial investments.
Advantages:
Reduced Production Steps and Costs: This method consolidates the injection of multiple materials into one cycle, eliminating subsequent processes and lowering both production costs and time.
Enhanced Product Quality: Two-shot molding can produce more durable, structurally stable products. The integration of two materials can improve overall performance, such as impact resistance and sealing properties.
Design Flexibility: It allows designers to combine different colors or types of plastics in one component, offering unique visual and tactile qualities.
Disadvantages:
Higher Mold Costs: The complex requirements for two-shot molds result in higher costs. Designing and manufacturing these molds demand extensive experience and precision, significantly increasing initial investments compared to traditional molding techniques.
Increased Production Hourly Rates: Specialized two-shot molding machines are more expensive than standard injection molding machines. Additionally, operating these machines requires specialized skills, contributing to higher hourly rates.
Environmental Concerns: Utilizing two distinct materials complicates recycling efforts, as effectively separating these materials can be challenging. The complexity of recycling and the inability to reuse production rejects pose significant challenges for two-shot molding.
Mold Requirements for 2 Shot Molding
Two-shot molding, a sophisticated injection molding technique that simultaneously uses two different materials or colors in the same molding process, demands highly precise molds. Ensuring the success of this process involves strict control over several aspects.
Alignment Precision
The precision of mold alignment is crucial. Two-shot molding employs molds that include two sets of lower molds (moveable) and two sets of upper molds (stationary), which need to rotate or shift during the molding process to align interchangeably. It is essential to ensure that both sets of molds are completely consistent in terms of outer dimensions, internal cavities, and height.
Typically, a CMM (Coordinate Measuring Machine, a three-dimensional measuring equipment) is used in production to check the precision of the molds, preventing injection molding defects such as flash due to misalignment.
Rigorous Mold Design and Review
The mold design and review process must be highly meticulous. Given the high cost of two-shot molds, any flaws in the design could lead to modifications in both sets of molds, thereby incurring additional costs. Therefore, the design stage of the molds must carefully consider various elements, including the design of gates and runners, the arrangement of sliders, and the layout of the cooling system. These aspects require thorough verification and validation to ensure no oversight.
Automatic Degating
Considering the emphasis on production efficiency in two-shot molding, mold designs should aim for automatic degating whenever possible. This means that at the end of the injection molding process, excess material from the injection ports can be automatically removed from the product without manual intervention. This reduces labor costs and enhances production efficiency.
Material Requirements for 2 Shot Molding
In two-shot molding, the bonding between the substrate and the overmolding layer is achieved through chemical and physical processes, involving material selection, mold design, and processing conditions. This bonding process ensures that two different materials tightly integrate in the final product, forming a structurally intact and functionally robust composite. Here are several key factors in this bonding process:
Material Selection and Compatibility
Choosing compatible materials is crucial for a successful bond. The substrate and overmolding materials must be compatible in their molten states without adverse chemical reactions. Material suppliers often provide guidance on which material pairings achieve the best adhesion.
Surface Treatment
In some cases, the substrate’s surface may undergo special treatments such as sandblasting, chemical etching, or surface activation to increase its roughness and chemical reactivity, thereby enhancing the bond strength with the overmolding layer.
Mold Design
Mold design is also critical in ensuring a good combination of the two materials. The mold must precisely control the flow path of each material, ensuring that the second material forms a stable and uniform coverage over the first material’s surface.
Injection Molding Parameters
The parameters during the injection molding process, such as temperature, pressure, and cooling time, need careful adjustment to suit the characteristics of both materials. Proper temperature and pressure can promote good material bonding, while the right cooling time ensures that the materials solidify without internal stress, affecting the bond strength.
Molecular Diffusion
At the interface of the two materials in their molten state, molecular diffusion occurs, meaning molecules from one material penetrate into the other. This helps form stronger chemical bonds and physical entanglements, enhancing the adhesion between the two materials
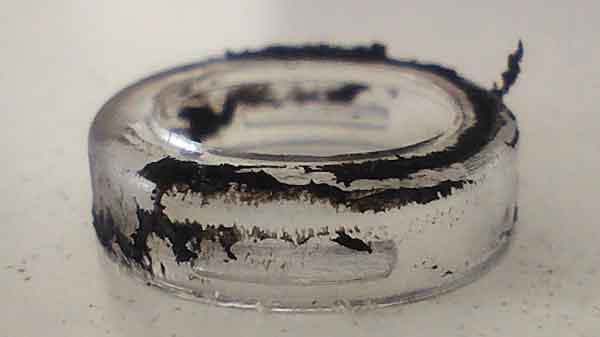
Commonly Used Materials
- Substrate Materials: ABS, PC, PC/ABS, PP, PMMA, PA6, PA66, etc.
- Overmolding Materials: TPE, TPU, Silicone, and hard plastic materials used as substrates.
Consulting with material suppliers is advisable to confirm the compatibility of the two materials.
Through the methods and mechanisms described above, two-shot molding can achieve a tight bond between the substrate and the overmolding layer, producing composite material products that are both aesthetically pleasing and high-performing. This technology is widely applied in various fields such as electronic devices, automotive parts, and medical instruments, offering more possibilities for product design and functionality.
Comparison Between 2 Shot Molding and Overmolding
When discussing two-shot molding technology, it’s common to compare it with overmolding. Though these two techniques seem similar in many aspects, involving multiple (two or more) injection molding processes, there are key differences between them.
Bonding Strength
- Two-shot Molding excels in this area. This technique ensures a tight bond between two materials in a continuous process. Since the substrate material from the first injection is not fully cooled, it’s easier for the molecular chains of the two materials to entangle and fuse, achieving a stronger bond. Additionally, two-shot molding ensures the cooling rates and shrinkage of both materials are more consistent, reducing separation due to mismatched material shrinkage.
- Overmolding requires manually placing the first injection molded part into another mold for the second injection, which might affect the tightness of the material bond.
Production Cost
- Two-shot Molding is more efficient, completing both injections in a continuous process. Although the hourly production cost might be higher, the overall efficiency could reduce the total production cost.
- Overmolding increases labor costs by requiring manual placement of the substrate part into another mold, and with the injections being separate processes, this could lead to higher overall processing costs. However, for small batch production, overmolding might be more suitable due to its lower initial investment.
Design Diversity
- Two-shot Molding offers greater design flexibility. Its unique production process allows for more complex designs to be realized during the second injection, such as activating sliders and lifters only after the second injection, providing a broader space for product design.
- Overmolding limits the possibility of reintroducing cores or sliders for complex structures once the substrate part is placed into the mold, somewhat restricting design diversity. Certain specific designs can only be achieved through two-shot molding and not overmolding.
Manufacturing Precision
- Two-shot Molding achieves higher positioning precision due to its continuous production process, which doesn’t require removing the substrate part from the mold, thus improving the overall manufacturing precision of the product.
- Overmolding introduces positioning errors when manually placing the first injection molded part into another mold, affecting the final product’s precision.
In conclusion, while both two-shot molding and overmolding serve to create composite materials through multiple injection processes, they each offer unique benefits suited to different manufacturing needs.
- Two-shot molding stands out for its superior bonding strength, design flexibility, and precision, ideal for large-scale, complex projects.
- Overmolding, on the other hand, offers cost advantages and simplicity, making it more suitable for smaller-scale or less complex applications.
Choosing between the two depends on specific project requirements, costs, and desired outcomes.
Conclusion
In summary, two-shot molding is an advanced injection molding technique that efficiently combines two different materials or colors in a single cycle, offering significant advantages in terms of design flexibility, product quality, and production efficiency. Despite its higher initial investment in mold design and machinery, the technology presents a compelling case for applications requiring complex, multi-material components with high precision and strength.