What is Thin Wall Injection Molding?
Injection molded parts are typically plastic products with thin and uniform wall thicknesses. While excessively thick walls can lead to certain issues, walls that are too thin also pose their own challenges.
This is primarily due to the cooling process: when molten plastic enters the mold, it rapidly solidifies. Thinner walls lead to faster cooling and higher flowing resistance, which can create a range of issues.
Wall Thickness Under 1mm – For most plastics, the “sweet spot” for wall thickness generally falls between 1.5mm and 3mm. When the wall thickness drops below 1mm, the part can be considered a thin wall product.
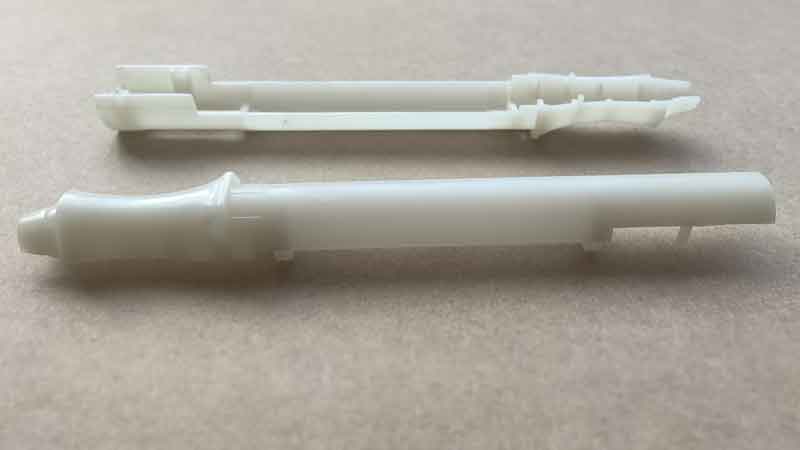
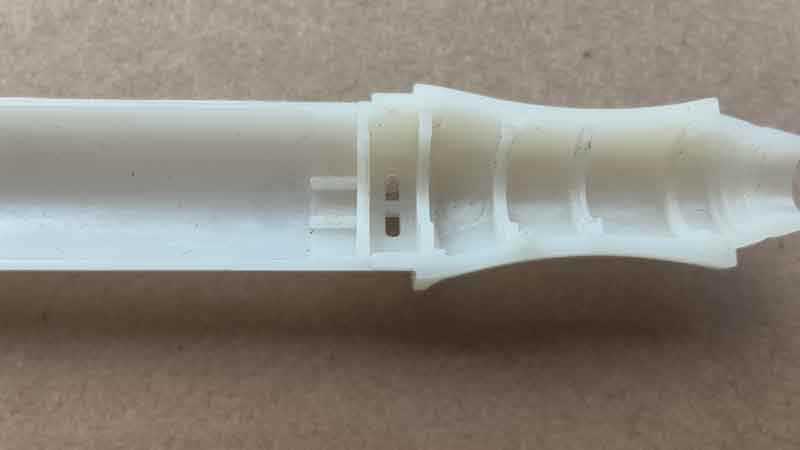
(This product has a wall thickness of 0.9mm. While simple and small thin-walled parts are not hard to make, the ribs pose many challenges. Continue reading to learn about the main issues in manufacturing thin-walled plastic parts.)
Of course, this is not an absolute rule. The minimum wall thickness is often determined by the size of the part. Smaller parts can be molded with thinner walls. For example, certain areas of a part might have wall thicknesses as thin as 0.2-0.3mm. However, for larger parts, such as those over 500mm, a uniform thickness of 1.5mm can still be considered quite thin.
This is a family mold for three transparent plastic discs. Note that the front disc is 1mm thick, while the two at the back are 2mm thick. Although the varying thickness adds some complexity to the injection molding, the small size, simple shape, and lack of features like tabs and ribs make the molding process relatively straightforward.
In this post, we will discuss the challenges faced when working with thin wall injection molded parts. We’ll also explore important considerations for designing plastic components, such as selecting the right materials and designing the part’s shape to minimize potential issues.
Why Choose Thin Wall Design?
In general, plastic part designs often tend to have thicker walls, but there are certain situations where thinner walls are required. Below are some key reasons to adopt a thin wall design:
Functional Reasons
- Flexibility: Sometimes, parts need a certain level of flexibility.
- Compact Design: For smaller products, such as electronics, maintaining a thin wall thickness is crucial for ensuring the compactness and integrity of the overall design.
(These are the buttons of a car key, made by 2-shot molding. Due to the requirement for light transmission through the white plastic and the need for a compact overall design, the wall thickness is kept quite thin.)
- Transparency: For transparent parts, certain materials (e.g., polypropylene) require thinner walls to maintain adequate transparency.
Cost Considerations
- Material Savings: For large-volume production, every gram counts! Reducing wall thickness not only cuts material costs but also helps decrease the injection molding cycle time. Since production efficiency is closely tied to processing costs, optimizing cycle time can lead to significant savings.
Common Issues and Solutions for Thin Wall Injection Molding
Thin wall parts are relatively easy to manufacture if the structure is simple, with minimal ribs and bosses, a large draft angle (which makes demolding easier), and few holes. However, if these factors are not considered, the difficulty of injection molding increases, and the likelihood of issues arising also grows. In general, thin wall injection molded parts may encounter the following problems:
Product Shrinkage Smaller Than Expected, Leading to Oversized Parts
Thin-walled products cool and solidify more quickly, causing the material’s shrinkage rate to be lower than usual. This results in the final product being larger than anticipated.
Solution: During the design phase, it’s important to account for potential changes in shrinkage ratios. Mold flow analysis can help predict this, and having prior experience with similar products is invaluable in making accurate assessments.
For example, in one case, the part was made from reinforced nylon, which typically has a shrinkage rate of 0.5% (based on a range of 0.3-0.8%). However, in practice, its shrinkage rate was only about 0.2%, and extending the holding time didn’t bring it closer to 0.5%. We eventually switched to pure nylon, which has a typical shrinkage rate of around 1.2% (within a range of 1.0-1.5%). The actual shrinkage rate of the pure nylon was 0.5%, meeting the required dimensions. If material substitution is not feasible, modifying the mold is the only solution.
Local Deformation and Whitening Marks, or Even Complete Deformation
This issue typically occurs in areas with tall side walls, ribs, and bosses that have a small draft angle. The thin wall thickness reduces the part’s strength, making it unable to withstand the ejection force, leading to material deformation and whitening. In more severe cases, the part can become completely deformed or even broken.
Solution: To address this, you can reduce the height of side walls, ribs, and bosses, increase the draft angle, and polish the mold surface in these areas to reduce ejection resistance. Additionally, extending the cooling time during injection molding allows the part to solidify more before ejection, reducing the likelihood of deformation.
Short Shot: Material Insufficient in Some Areas
Due to the thinner wall thickness, the flow resistance increases, which can lead to material shortages in certain areas of the part.
Solution: To resolve this, you can increase the mold and material temperature to improve flowability. Improve venting and increase the size of the injection gates. Additionally, increasing injection pressure and speed can help. It’s also beneficial to use materials with better flowability, such as PP, PA, or PE.
Weld Lines: Visible Lines Due to Faster Cooling
Due to the faster cooling of thinner walls, weld lines are more likely to form, especially around holes, resulting in visible marks.
Solution: To minimize weld lines, increase the mold and material temperatures. Using PP material can generally avoid weld lines, although some applications may not meet gloss, strength, or other requirements. Increasing injection pressure and speed can also help. Additionally, this requires molds with higher precision to prevent the formation of flash.
Mottling: Sensitivity to Discoloration in Thin Wall Parts
Thin wall products are more sensitive to mottling. Sometimes this is caused by the injection of cold material during the molding process, but there are also other complex reasons, such as material degradation due to prolonged exposure to high temperatures. While we can only offer a general explanation here, the issue is multifaceted.
Solution: To address this, you can incorporate cold runner wells in the mold and use a hot runner system to avoid cold material. In small batch production, it may even be necessary to purge the nozzle between each injection cycle to clear out cold material or other defective material. However, this increases operational complexity and injection molding costs, making it a less common practice.
Thin wall products are more sensitive to mottling. Sometimes this is caused by the injection of cold material during the molding process, but there are also other complex reasons, such as material degradation due to prolonged exposure to high temperatures. While we can only offer a general explanation here, the issue is multifaceted.
Solution: To address this, you can incorporate cold runner wells in the mold and use a hot runner system to avoid cold material. In small batch production, it may even be necessary to purge the nozzle between each injection cycle to clear out cold material or other defective material. However, this increases operational complexity and injection molding costs, making it a less common practice.
Design Considerations for Thin Wall Injection Molding Parts
If you’re not particularly familiar with injection molding processes, it’s important to understand the challenges thin wall designs present and plan accordingly during the design phase.
Use Materials with Good Flowability
The flowability of commonly used thermoplastic plastics can generally be categorized into three levels:
- Good Flowability: PA (Polyamide), PE (Polyethylene), PS (Polystyrene), PP (Polypropylene), CA (Cellulose Acetate), etc.
- Average Flowability: ABS (Acrylonitrile Butadiene Styrene), PMMA (Polymethyl Methacrylate), POM (Polyoxymethylene), PCE (Polychloroether), etc.
- Poor Flowability: PC (Polycarbonate), PVC (Polyvinyl Chloride – Rigid), PPO (Polyphenylene Oxide), PSU (Polysulfone), PTFE (Polytetrafluoroethylene), etc.
Design Considerations for Parts with Thin Walls
If the plastic part has a box-like structure, meaning it has side walls, you should consider reducing the height of the side walls or increasing the draft angle. This helps reduce the ejection resistance of the part.
Additionally, reduce the height of ribs and increase the draft angle. For more details on wall thickness design, refer to our other post dedicated to this topic.
Contact Us If You Need Help
Of course, these are just general guidelines. When lacking sufficient experience in injection molding and mold design, external assistance is often needed. If you require a more detailed evaluation or modifications to your thin wall part designs, Boyan is here to help. Please feel free to contact us immediately.